Updated on March 5, 2020 by Brian Hughes
Month: July 2015
Fanuc A06B-6050-H103 Servo Jumper Settings
When replacing a Fanuc A06B-6050-H103 Servo unit you should check to make sure the replacement servo has the same top board, part number A20B-1000-0560. After this part number there will be a “/” and then something similar to “05A” which denotes the revision of the board. Ideally you would match your original unit with a replacement unit that has the same board, but if that’s not possible then all you would need to do is reconfigure the jumpers on the board. The table below shows how to get this set up so you can get your servo back up and running right away. Search for more FANUC motors/drives on our website.
MRO Electric and Supply maintains a comprehensive stock of new and used FANUC CNC and FANUC Robots parts. If you need a FANUC replacement part, please call 800-691-8511 or email sales@mroelectric.com.
Updated on March 5, 2020 by Brian Hughes
Fanuc Alarm 466 – Z Axis: Motor/Amp Combination
We just shipped out a Fanuc A06B-6096-H207 Servo Amp unit to a customer, and as soon as they installed the amplifier they got a Fanuc Alarm 466 which refers to the Z Axis: Motor/Amp Combination. This is obviously somewhat distressing for a customer to buy a replacement unit and immediately get an alarm when it is installed, but fortunately this is an easy fix.
This Alarm 466 comes from the replacement amplifier having newer servo software than the unit that it is replacing. As Fanuc has made newer units they’ve upgraded the software/hardware within these amplifiers, so you just need to reset a parameter to reboot the configuration and clear the 466 Alarm. The steps are below.
– Put the machine in Emergency Stop
– Go to parameter 2165 on the control
– Set all the values to 0
– Take the machine out of emergency stop
Once these parameters are changed and the machine is rebooted, the alarm will clear and the amplifier will initialize. We also have pictures below to confirm that you know what to look for. For any additional help, call us at 800-691-8511 or email sales@mroelectric.com.
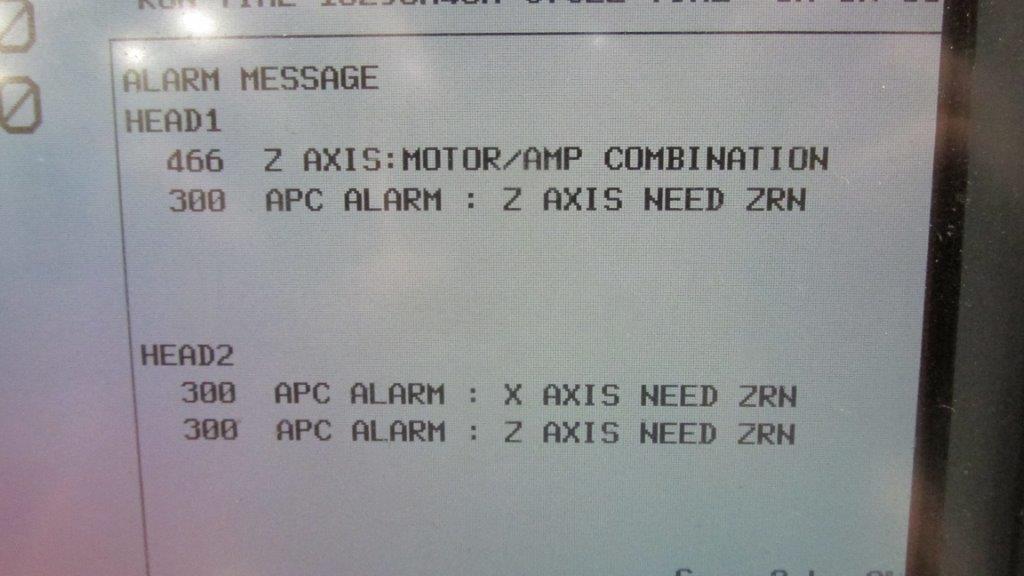
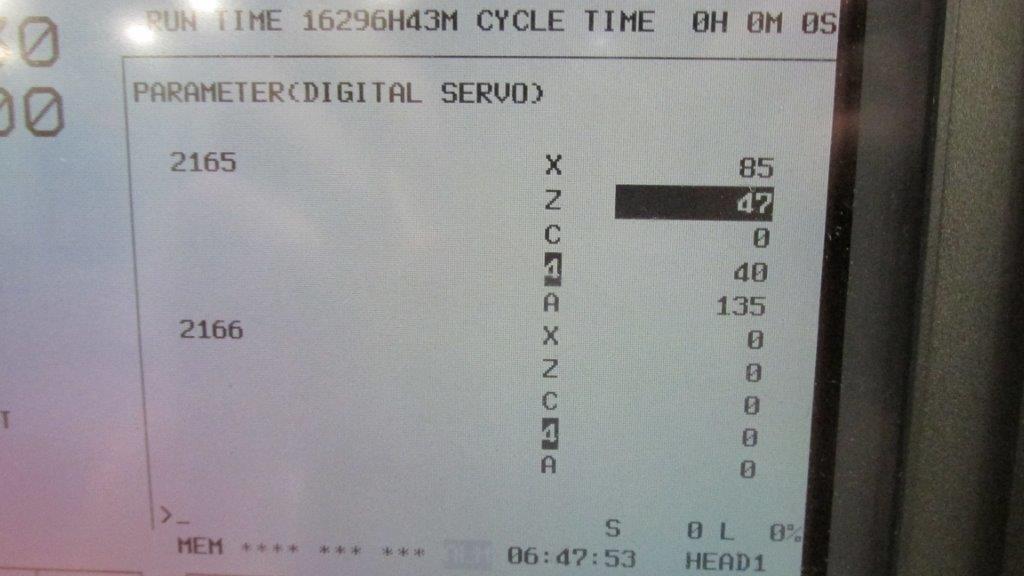
MRO Electric stocks a large number of FANUC CNC Products, and provides repair services as well. For more information or to request a quote, please call 800-691-8511 or email sales@mroelectric.com.
Updated on March 5, 2020 by Brian Hughes