Some sports fans take a loss in stride, while others…not so much. Whether it’s blaming the refs, talking trash even after the final whistle, or full-blown meltdowns, certain states’ sports fans just feel a defeat more deeply. With high-stakes games and bracket-busting upsets fueling emotions this time of year, the intensity is at an all-time high.
To find out which states have the sorest losers, we surveyed over 2,100 sports fans nationwide, asking them about the sportsmanship—and not-so-sportsmanlike reactions—of fans in their state. The results reveal which states take losses way harder than others.
States Most & Least Likely to Be Sore Losers
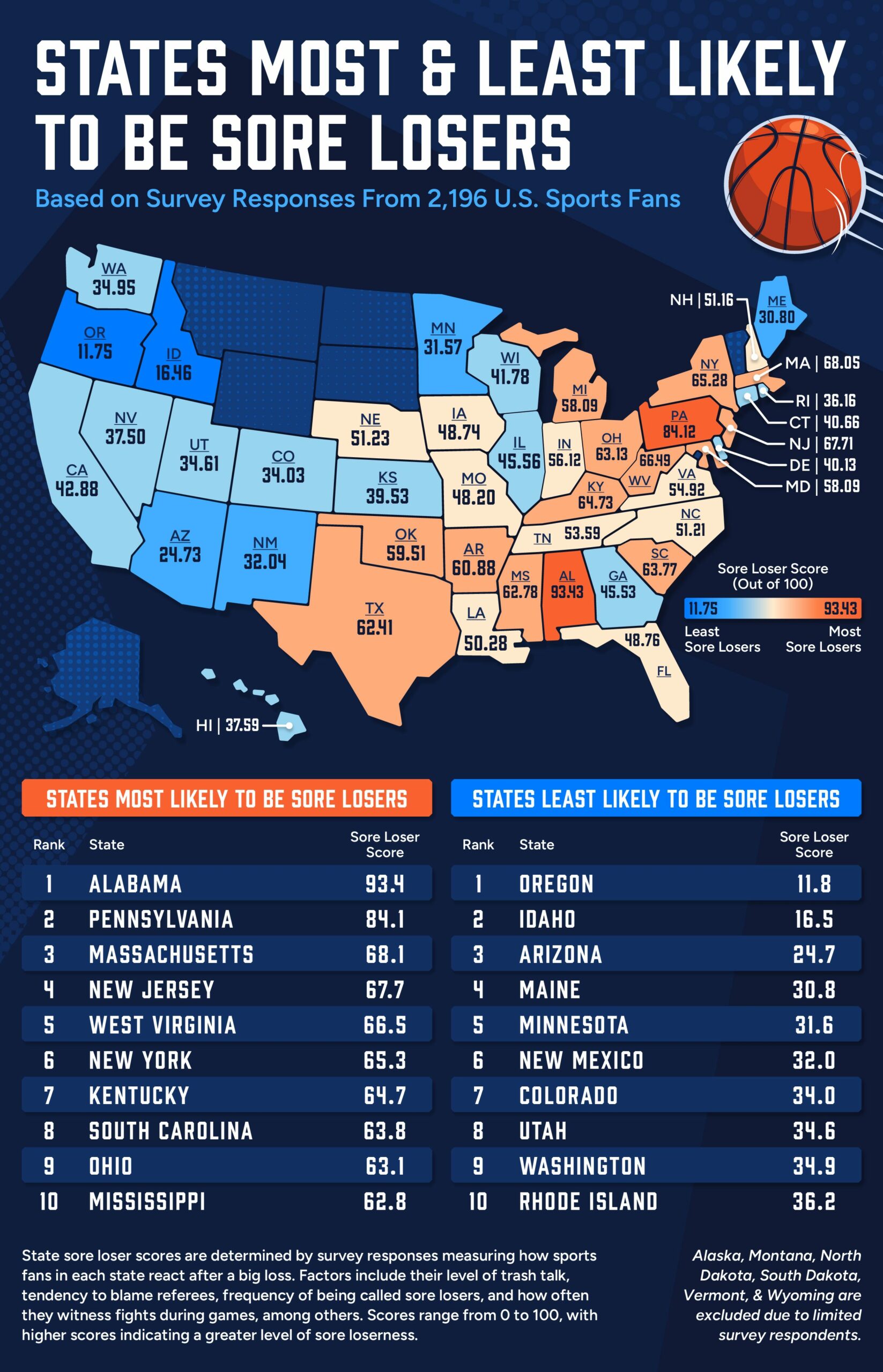
We surveyed sports fans across 44 U.S. states, asking 10 questions to gauge their level of sportsmanship, competitiveness, and just how hard they take a big loss. The survey measured everything from trash-talking habits to how often fans blame the refs, whether they’ve been called a sore loser, and even how frequently fights break out during games. Each question was answered on a 1-to-5 scale, with 5 indicating a higher likelihood of sore loser behavior. We then averaged the responses and indexed them into a final sore loser score out of 100 for each state—with higher final scores signaling states where taking an “L” hits the hardest.
These are the five states with the sorest losers, and their respective sore loser scores (out of 100):
- Alabama – 93.4
- Pennsylvania – 84.1
- Massachusetts – 68.1
- New Jersey – 67.7
- West Virginia – 66.5
When it comes to taking a loss very personally, no one does it quite like Alabama. Topping the list with a sore loser score of 93.4, Alabama sports fans bring an unmatched level of passion to every matchup. And when the scoreboard doesn’t go their way? Let’s just say they feel it. More than half of Alabamians (51%) admit to having a total meltdown after a big loss—the only state in the survey where this was the most common reaction. And if you’ve ever heard “the refs blew it!” echoing through an Alabama bar or living room, that checks out too: 33% say they “almost always” blame losses on bad calls, while 41% say they do it “often.” What’s more, 43% of Alabama respondents say they’ve witnessed a sports fan throw a tantrum after a loss more times than they can count.
That intensity isn’t just reserved for college rivalries—it starts early. Alabama parents bring just as much energy to the sidelines of youth sports. A quarter of Alabama respondents (25%) say parents in their state “almost always” get too worked up at kids’ sporting events, while 37% admit they do so “often.” Whether it’s a Saturday in Bryant-Denny or a little league game in Birmingham, one thing is clear: Alabama takes its sports very seriously.
Trailing behind but still bringing the drama are Pennsylvania, Massachusetts, New Jersey, and West Virginia—all states where sports are treated with near-religious devotion. When asked, “Which best describes your state’s sports fanbase?” Pennsylvania respondents were the most likely to choose “We talk trash before and after the game, win or lose”—a sentiment shared by nearly 60% of them. And that competitive spirit doesn’t always go unnoticed. Half of Pennsylvania respondents admit they’ve been called a sore loser at least once or twice, while in neighboring New Jersey, 45% of respondents say the same.
Over in Massachusetts, nearly half of respondents say sports are taken “extremely seriously—every game feels like a big deal.” But if you’re looking for high-intensity matchups, West Virginia might take the crown. More than half (54%) of respondents in the state have witnessed a fight break out during a game they were playing in. And the passion starts early—15% of West Virginia respondents say parents in their state “almost always” get too worked up at kids’ sporting events, while 38% say it happens “often.”
On the opposite end of the spectrum, these are the five states least likely to be sore losers, and their respective sore loser scores (out of 100):
- Oregon – 11.8
- Idaho – 16.5
- Arizona – 24.7
- Maine – 30.8
- Minnesota – 31.6
Some states accept losses with a bit more grace than others. According to survey results, Oregon is the least likely state to be full of sore losers, with a sore loser score of just 11.8. And the numbers back it up: 56% of Oregonians have never been called a sore loser, and when their team takes a big loss, 67% say they’re unbothered or don’t care at all, simply shrugging it off with an “it’s just a game” mentality. Even trash talk is kept to a minimum—a third (33%) rarely or never talk smack after a loss. And if you’re looking for sports parents who keep their cool, Oregon is the place to be. Not a single respondent said parents in their state “almost always” get too worked up at kids’ sporting events, and only 13% said it happens “often.”
Arizona and Idaho also rank among the least sore loser-prone states, with nearly half of respondents (48% in AZ, 47% in ID) saying they’ve never been called a sore loser. Idaho, in particular, leads the nation in sportsmanship—32% say they’ve never seen a fan throw a tantrum after a loss, the highest percentage of any state. Meanwhile, over in Maine, 64% of respondents say sports fans there don’t dwell on losses, and in Minnesota, 63% describe their fanbase as “passionate but mostly respectful.” Minnesotans also keep their cool in the heat of the game—67% say fights during games almost never break out, while another 20% say it’s rare.
Full State-by-State Ranking
Curious about where your state ranks? Our interactive table below breaks down the full survey results, showing the most common answers for all 10 sore loser-focused questions in each state. You can search for your state or sort by different categories to see which fanbases take losses the hardest—and which ones truly let it go.
Closing Thoughts
At the end of the day, some states take sports losses harder than others—and our survey proves it. Alabama, Pennsylvania, and Massachusetts top the list as the sorest losers, where fans are more likely to blame the refs, talk trash after a loss, and even witness full-blown meltdowns. Meanwhile, Oregon, Idaho, and Arizona keep things cool, proving that not every fanbase lets a tough defeat ruin their day. Whether your state lives for the thrill of competition or takes an “it’s just a game” approach, one thing is clear: sports bring out strong emotions, win or lose.
Just like sports fans rely on their teams to show up and perform, businesses rely on industrial automation systems to keep things running smoothly—because downtime is never an option. At MRO Electric, we specialize in repairing and supplying industrial automation components, helping businesses maintain peak performance even under pressure. Get in touch with us today to keep your operations running at championship level.
Methodology
To find the states with the sorest losers, we conducted a survey of 2,196 U.S. sports fans across 44 states. The survey ran over a one-week period, from February 12 to February 19, 2025. Alaska, Montana, North Dakota, South Dakota, Vermont, and Wyoming were excluded from the survey due to limited survey respondents in those states.
For the state ranking portion of our study, we evaluated states across 10 key survey questions that reflect sore loser behaviors, ultimately measuring how sports fans in each state react after a big loss. Questions included their level of trash talk, tendency to blame referees, frequency of being called sore losers, and how often they witness fights during games, among others. Each question was answered on a 1-to-5 scale, with 5 indicating a higher likelihood of sore loser behavior. We then averaged the responses and indexed them into a final sore loser score out of 100 for each state—with higher final scores signaling states most likely to be sore losers.