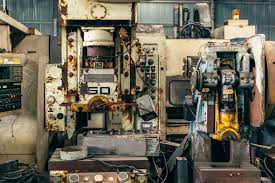
Upgrading Vs Swapping
When it comes to the world of automation controllers, it is important that a system perform as long as it possibly can. After all, what good is buying a new machine when a company has to shell out millions every few years for a full replacement? That being said, like all things, these systems have their own expiration date. Of course, that expiration time is not an exact number and very much depends heavily on multiple factors. Depending on the facility, management, operator, etc., an entire setup can potentially last up to 30 years if well maintained. In fact, while we are in the year 2022, there are numerous companies today that are still using equipment from the 1980’s with some going back further than that!
“When Should I Upgrade?”
Upgrading your system is a large undertaking for any company. Not only is the cost to upgrade something to really consider. Businesses also have to account for operations, deadlines, and return on investment (ROI). When thinking about upgrading your equipment, some important factors to think about include:
Production Challenges
If you are seeing a higher volume in sales and your current setup cannot meet the rise in demand, then it may be time to consider upgrading. Newer machines can output product at a faster rate.
Labor
Labor is often one of the largests costs when it comes to business operations. Not only are we talking about the base wage of an employee, but also the cost of training. Some fields of work have high turnover rates which makes having to hire and train new employees a constant and expensive venture. Some uprgrades are available that now automate certain tasks once perfomed by employees.
Cost
While the upfront cost might end up being quite a steep price to pay. In the long term, upgrading your equipment can give a business the competitive edge it needs to produce products faster, higher quality, and more efficiently thus saving money on the back end.
Expansion
As a company expands, the prospects of upgrading and automating certain aspects of the production is can not only help saving money in any long-term costs that comes with expansion, but also maintain quality control as the company grows.
Waste
The production of waste is not only an issue that comes with potential environmental and legal rammifications, but also with economical ones as well. The accountability of letting environmental waste go unchecked has long-lasting and very expensive repurcussions. Upgrading to newer equipment can also mean a reduction in waste production as well.
Better Precision
Newer equipment also tends to be more precise with higher accuracy in manufacturing which aids in the produciton of more complex components.
“What if Upgrading Isn’t Worth It?”
As previously mentioned, the greatest obstacle when it comes to upgrading is the upfront costs. Usually companies with enough capital can make these upgrades. Some companies with more limited capital may make incremental upgrades. However, there are plenty of businesses out there that simply do not have the sort of capital needed to commit to upgrading their equipment. This is especially challenging when a company’s equipment suddenly breaks down and needs replacing. The dire need for operations to continue means small turn around times (if any) for machines to be shut down. While this is happening, a company can lose huge sums of money from not having product to sell. Therefore many companies want whatever the quickest turn around time possible to get production back up.
One alternative solution for companies with smaller budgets is to just buy refurbished and certified pre-owned equipment from vendors. The advantage of this being that most components are able to be hot swapped. This allows you to just purchase and replace the broken part and not have invest in completely new machinery. Another advantage of this is that a company can save a lot of time and money by not having their technician needing to learn an entirely new system. Especially when going from a setup that was installed 30 years ago to the newest one.
The End Cost
It is important to take note that when replacing with pre-owned/used parts, these are in fact; used. It is good to make sure a refurbished vendor tests the product before selling it. Some vendors offer, warranties and have return policies in place. That being said, you’re still working with old equipment. The lifespan of used or refurbished items will not have the same longevity as new parts. This means the cost you were hoping to save by a simple part replacement may again end up costing you more down the road.
Ultimately, it is up to the owner to weigh the pros and cons. Afterwards they have to think about long vs short term solutions and if the cost is worth it.
Updated on March 7, 2023 by Ken Cheng