Through industrial automation, manufacturing has come a long way. The leaps and bounds in speed, precision, safety, and overall efficiency has vastly improved from earlier industrial age. One of the attributions to this success easily goes to the teach pendant. The invention of this handheld controller has allowed operators to program and troubleshoot a lot of problems with ease. In this article, we explore the role of teach pendants in automation, their key features, and their impact on modern manufacturing.
Read more: Teach Pendants in Industrial AutomationWhat is a Teach Pendant?
A teach pendant is a handheld control terminal used to program and operate industrial robots. It typically consists of a display screen, buttons, joysticks, and emergency stop functions. Operators use teach pendants to manually guide robots through tasks, define movement paths, set parameters, and store instructions for automated operations. This process is where teach pendant derives its name from.
Key Functions of a Teach Pendant
Teach pendants offer a multitude of functions making it possible for them to complete variety of tasks. Here are some examples of the function of teach pendants.
- Teach pendants allow for easy creation and editing of robotic programs. Waypoint and motion sequences can be recorded for repetitive task such as welding and assembly.
- Operators can have precise control over equipment movements via joystick or directional buttons.
- Teach pendants provide real-time feedback, error messages, and system status updates to quickly diagnose issues.
- Emergency stop buttons and dead-man switches ensure safe operation by halting robot movement instantaneously.
- Operators can fine-tune speed, torque, and trajectory settings to optimize performance.
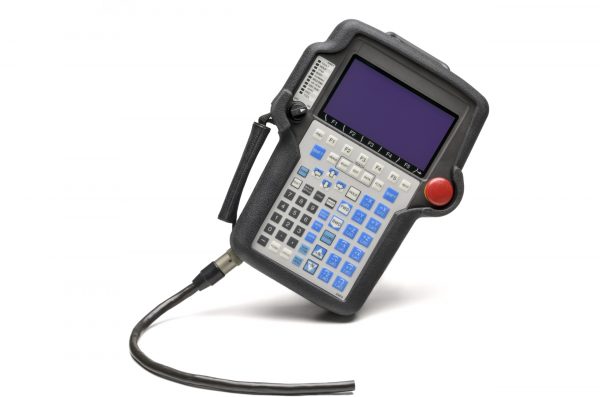
Advantages of a Teach Pendant
Teach pendants bring with them a lot of advantages that generally do not come with traditional control systems. For starters, teach pendants are made to be easily user-friendly and intuitive making it easy to train someone on. There’s a level a flexibility that they offer when it comes to programming and changing production settings. An operator can adjust between high and low volume production outputs.
Teach Pendant Types
- Wired Teach Pendants – Connected directly to the robot controller, ensuring reliable communication.
- Wireless Teach Pendants – Offer greater mobility but may have latency or interference concerns.
- Brand-Specific Pendants – Companies like FANUC, ABB, KUKA, and Yaskawa design proprietary pendants tailored to their robots.
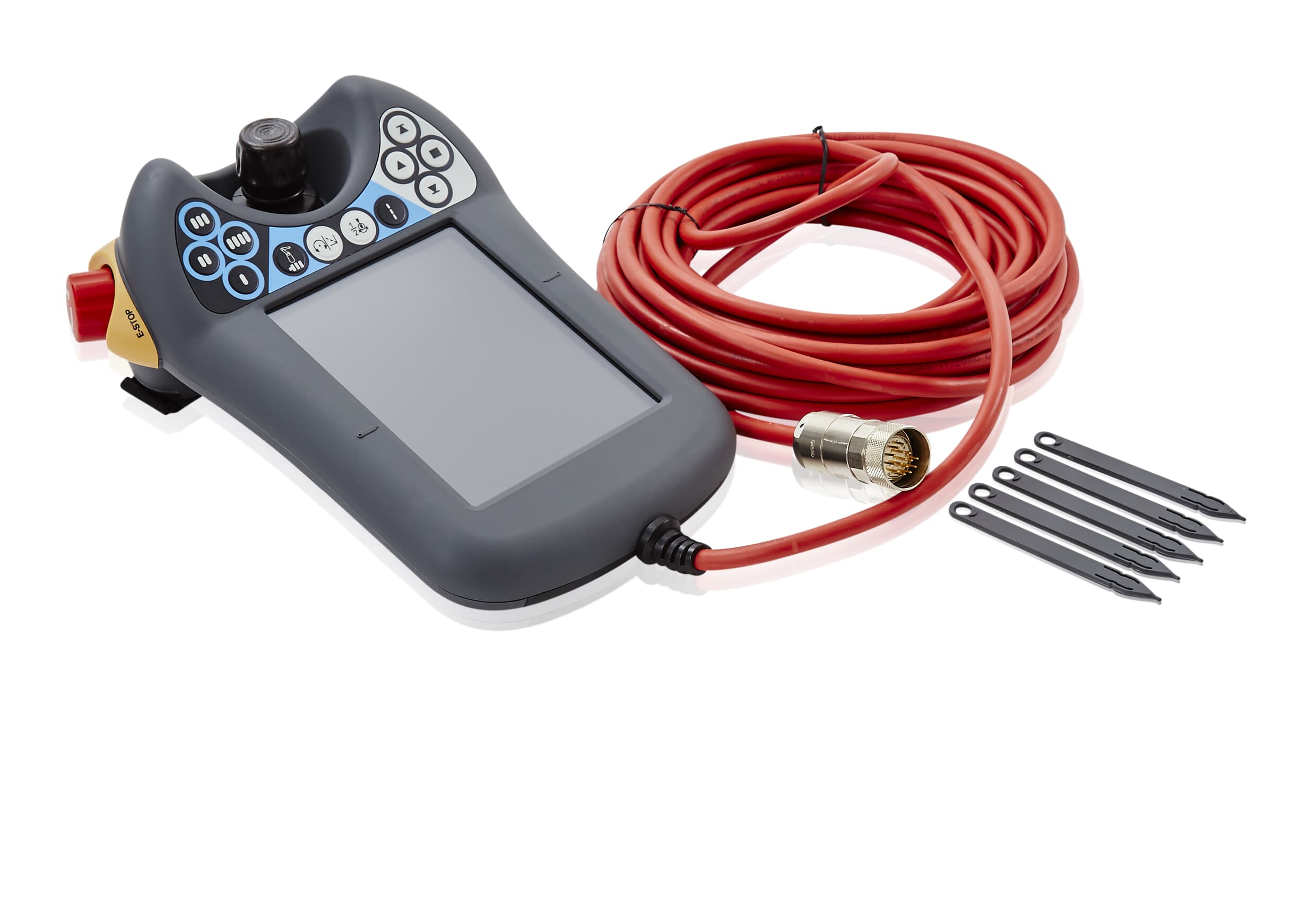
Conclusion
Teach pendants remain indispensable in industrial automation, bridging the gap between human operators and robotic systems. As technology advances, these devices will continue to enhance productivity, safety, and adaptability in smart factories worldwide.
By understanding their functionality and benefits, manufacturers can maximize the potential of robotic automation and stay competitive in an increasingly automated industry.
In Need of a Teach Pendant
With a large selection of FANUC, ABB, and KUKA teach pendants, we should have controller that fits your operating needs. Reach out to our team of experts and let us help you optimize your automation experience.
Learn About Servo Amplifiers
If you’d like to learn more about servo amplifiers, you read more about them here!