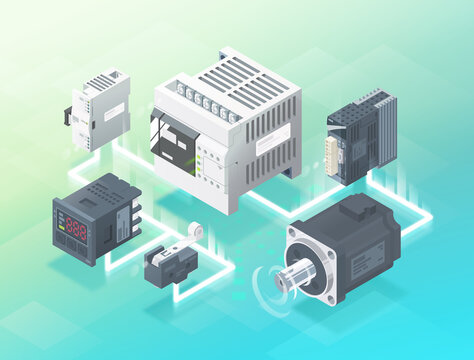
Programmable Logic Controllers (PLCs) play a crucial role in controlling and monitoring various processes. PLCs are versatile devices designed to automate electromechanical processes, replacing traditional relay-based control systems. Understanding the key components of a PLC is essential for engineers and technicians working in automation. Generally, four main components that make up a PLC.
Read more: Components of a PLCWhat is a PLC
In the past we’ve covered PLC’s and what they are, as well has how they function. The basic run down of a PLC is that it is a specialized industrial computing device designed to control and automate various processes within manufacturing and industrial environments. It serves as the brain of an automated system, executing programmed instructions to manage machinery, production lines, and other electromechanical processes. PLCs offer flexibility and versatility, enabling engineers and technicians to modify and adapt control logic easily without the need for extensive rewiring or hardware changes.
At the core of a PLC is its Central Processing Unit (CPU), responsible for executing control programs stored in memory. The CPU reads and interprets the instructions, making decisions based on the programmed logic. It then sends signals to output devices such as motors, valves, and sensors. Input modules gather data from the field through various sensors and switches, converting analog or digital signals into a format that the PLC can comprehend. Conversely, output modules translate the processed information from the CPU into signals that control the physical components of the automated system.
The Four Components
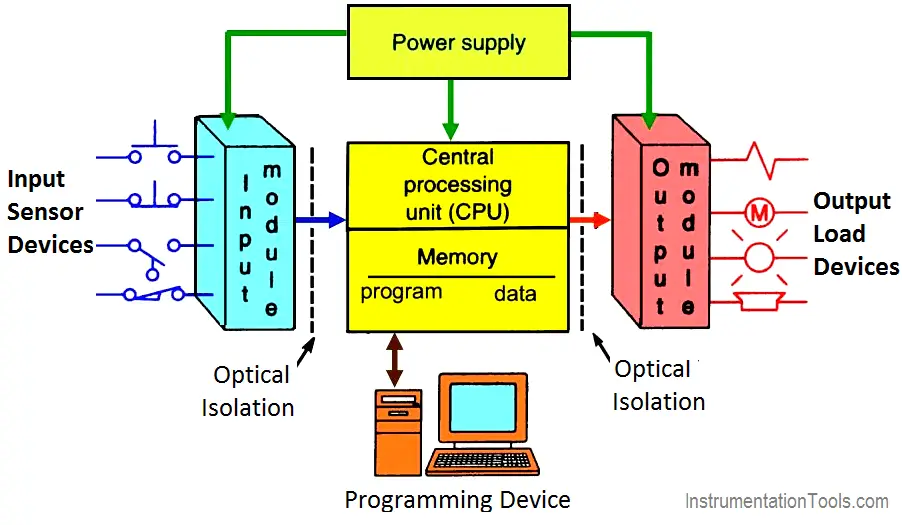
Central Processing Unit (CPU)
At the heart of every PLC is the Central Processing Unit (CPU). This component is the brain of the PLC, responsible for executing control programs and processing inputs and outputs. The CPU reads the program from memory, interprets the instructions, and sends signals to the output devices based on the program’s logic. Modern PLCs come with powerful CPUs capable of handling complex control tasks and communication with other devices on the industrial network.
Input Modules
Input modules are responsible for interfacing the PLC with the external world by collecting data from various sensors and switches. These modules convert analog or digital signals from field devices into a format that the PLC can understand. Digital input modules handle binary signals (on/off). In contrast, analog input modules process continuous signals such as voltage or current. Input modules are crucial for monitoring the state of the controlled system and providing real-time feedback to the PLC’s CPU.
Output Modules
Output modules facilitate communication between the PLC and the external devices such as motors, valves, or actuators. These modules convert signals from the CPU into a form that can control the physical processes in the industrial environment. Just like input modules, there are digital output modules for binary control and analog output modules for continuous control. The accuracy and reliability of output modules are vital for ensuring that the controlled system responds appropriately to the PLC’s commands.
Memory
PLCs have two types of memory: RAM (Random Access Memory) and ROM (Read-Only Memory). RAM is used for storing the control program and data temporarily while the PLC is powered on. ROM contains the firmware and the operating system that are essential for the PLC’s functionality. The memory capacity of a PLC varies, and it is crucial to choose a PLC with sufficient memory to accommodate the complexity of the control program and the amount of data processing required.
Conclusion
Programmable Logic Controllers have revolutionized industrial automation, providing a robust and flexible solution for controlling and monitoring complex processes. Understanding the four main components of a PLC – CPU, Input Modules, Output Modules, and Memory – is fundamental for anyone working in the field of industrial automation. As technology advances, PLCs continue to evolve, incorporating new features and capabilities. Furthermore PLCs enhance their role in modern manufacturing and industrial processes.
Updated on March 13, 2024 by Ken Cheng