In 2025, the landscape of industrial automation and precision motion control is being redefined by innovations in servo amplifier technology. As smart manufacturing, servo amplifiers have undergone a significant transformation to meet the rising demands for speed, efficiency, and intelligence.
Read more: Servo Amplifier Innovations in 2025How Servo Amplifiers Have Changed
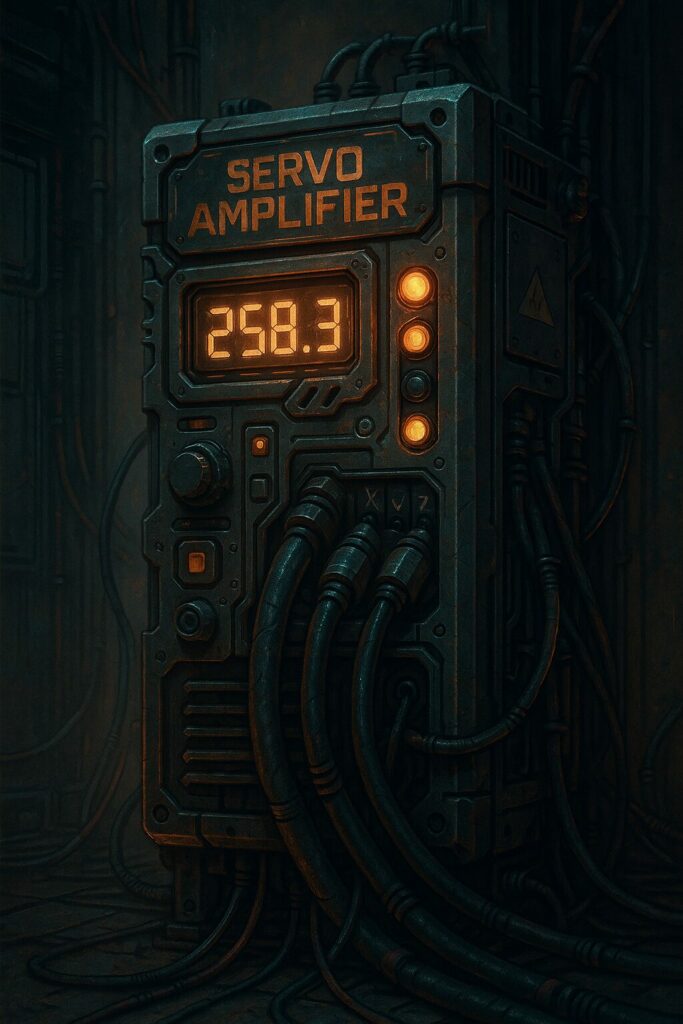
In the Past
Older servo amplifiers, commonly used in mid-to-late 20th century industrial and military applications, were primarily analog devices. These devices relied on operational amplifiers (op-amps), transistors, and thyristors (SCRs) to control motor position, speed, or torque. These amplifiers used feedback signals from resolvers, tachometers, or potentiometers to compare the actual motor performance with the commanded input. The error signal was amplified and used to adjust the motor’s power supply. This was done typically via pulse-width modulation (PWM) or linear amplification in high-precision systems.
Power regulation in these systems was often achieved using linear amplifiers for low-power applications or phase-controlled rectifiers (SCR-based) for higher-power motors. Linear amplifiers provided smooth, low-noise output but were inefficient due to significant heat dissipation. SCR-based amplifiers improved efficiency by switching high currents at precise phases of the AC input waveform, though they introduced more electrical noise and required careful tuning to avoid instability in the servo loop.
No Digitalization
Older servo amplifiers lacked modern digital processing, meaning tuning and compensation (such as PID control) had to be manually adjusted using potentiometers and RC networks. This made them sensitive to temperature drift and component aging. Despite their limitations, these systems were robust and provided sufficient performance for many early CNC machines, radar systems, and industrial automation tasks before digital signal processors (DSPs) and microcontrollers revolutionized servo control in the 1980s and beyond.
Servo Amplifiers of 2025
Today’s servo amplifiers have come a long way since their 20th century counterparts. These new servo amplifiers leave smaller environment footprints and built more energy efficient.
Smaller Footprints
One of the most notable trends in 2025 is the drastic reduction in the size of servo amplifiers without compromising performance. Thanks to advancements in power electronics, including the widespread adoption of silicon carbide (SiC) and gallium nitride (GaN) semiconductors, modern servo amplifiers offer higher switching frequencies, reduced heat generation, and more compact form factors. This makes them ideal for tight spaces in collaborative robots (cobots), mobile platforms, and micro-automation environments.
AI
Servo amplifiers have grown smarter. Many new models now feature embedded AI and machine learning algorithms that allow for auto-tuning, adaptive control, and predictive maintenance. These amplifiers can analyze motor performance in real time, detect anomalies, and even predict component failure before it happens. This leads to lower downtime, longer equipment life, and significantly improved OEE (Overall Equipment Effectiveness).
Cloud and Edge Connectivity
Modern servo amplifiers are increasingly designed with native Ethernet-based protocols (like EtherCAT, PROFINET, and Ethernet/IP) and support for edge computing. Some amplifiers even feature built-in web servers for remote access, configuration, and monitoring. This level of connectivity enables seamless integration into industrial IoT (IIoT) ecosystems and real-time data sharing with MES and ERP systems.
Energy Efficiency and Regenerative Capabilities
As sustainability continues to drive industrial innovation, energy-efficient servo amplifiers have become a priority. New-generation amplifiers support dynamic energy regeneration, capturing kinetic energy during deceleration and feeding it back into the power supply or shared bus systems. Coupled with high-efficiency motor control algorithms, these amplifiers contribute to reduced energy costs and a smaller carbon footprint.
Universal Compatibility and Modular Designs
Many new models are motor-agnostic, capable of driving brushless DC (BLDC), stepper, and synchronous/asynchronous AC motors from a single unit. Modular designs allow engineers to scale systems up or down with minimal reconfiguration, speeding up development time and reducing inventory complexity for OEMs.
Integrated Cybersecurity
With increasing connectivity comes greater vulnerability. Recognizing this, manufacturers now embed cybersecurity features directly into servo amplifiers, including secure boot, encrypted firmware updates, and real-time network monitoring to guard against cyber threats. This is especially critical in sectors like aerospace, defense, and medical automation.
Conclusion
The evolution of servo amplifiers in 2025 is emblematic of the broader shift toward smarter, more connected, and sustainable automation technologies. As these amplifiers become more compact, intelligent, and energy-conscious, they will play an even greater role in shaping the next generation of high-performance machinery and robotics.
Whether you’re an automation engineer, OEM, or system integrator, staying abreast of these innovations will be key to building future-ready solutions.
Looking For a Servo Amplifier in 2025?
Are you in need of a servo amplifier? Reach out to our team of experts and let us help you get back up and running in no time!
Updated on July 28, 2025 by Ken Cheng