Programmable Logic Controllers (PLCs) are integral components in industrial automation, serving as the backbone for controlling machinery and processes. Understanding their lifespan is crucial for maintenance planning and system upgrades. While exact lifespans can vary based on factors such as operating conditions and technological advancements, industry observations provide valuable insights.
Read more: Average Lifespan of a PLCGeneral Lifespan Estimates
Discussions among industry professionals suggest that PLCs can operate effectively for approximately 10- 20 years. For instance, some facilities have reported PLCs functioning reliably for over 30 years before replacement. However, it’s essential to recognize that these figures are anecdotal and can vary based on several factors, including the specific model, operating environment, and maintenance practices.
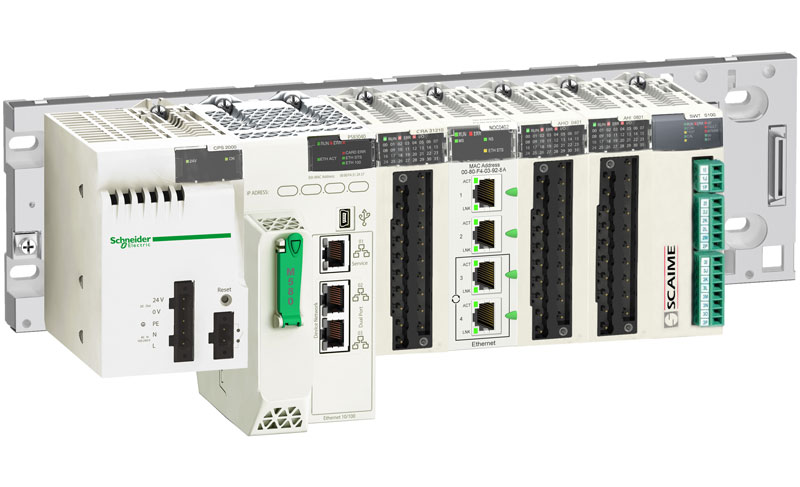
Factors Influencing PLC Lifespan
Several elements can impact the operational life of a PLC:
- Operating Environment: Units in a clean, temperature-controlled settings typically outlast those in harsh environments with extreme temperatures, dust, or moisture.
- Maintenance Practices: Regular maintenance and timely updates can extend lifespan by preventing issues that could lead to premature failure.
- Technological Advancements: As technology evolves, newer models with enhanced features become available, which might prompt upgrades even if existing units are still functional.
Prolonging PLC Lifespan
To optimize the lifespan and performance of PLCs, consider the following strategies:
- Standardization: Implementing standardized systems across facilities can simplify maintenance and training, leading to more efficient operations.
- Vendor Support: Engage with manufacturers to understand their support policies, ensuring access to necessary components and technical assistance throughout the lifecycle.
- Proactive Upgrades: Regularly assess the benefits of upgrading to newer PLC models, balancing the advantages of advanced features against the costs and potential disruptions of replacement.
Conclusion
While PLCs are designed for durability and can function effectively for decades, their actual lifespan depends on various factors. By considering operating conditions, maintenance practices, and technological developments, industries can make informed decisions to ensure the reliability and efficiency of their automation systems.
Need a PLC Replacement or Repair?
Do you have a PLC way past it’s lifespan and needs replacing? Our team of professionals can help you get your operation back and running in no time.