In today’s technology-driven world, our homes are filled with a plethora of electronic devices, appliances, and smart technologies. These advancements bring convenience and efficiency, but they also make our homes more vulnerable to power surges. A sudden surge in electrical voltage can damage or destroy electronic equipment. This leads to expensive repairs and replacements. For this reason, whole house surge protectors are an essential line of defense.
Read more: Whole House Surge Protectors: Pros and ConsWhat Happens During a Power Surge
A power surge is a rapid and temporary increase in voltage that exceeds the standard flow of electrical current in your home’s wiring. These surges can result from various sources like, lightning and power grid fluctuations. While minor surges may go unnoticed, repeated exposure to these events or a severe surge can cause irreparable damage to sensitive electronics.
What Goes Into a Whole House Surge Protector
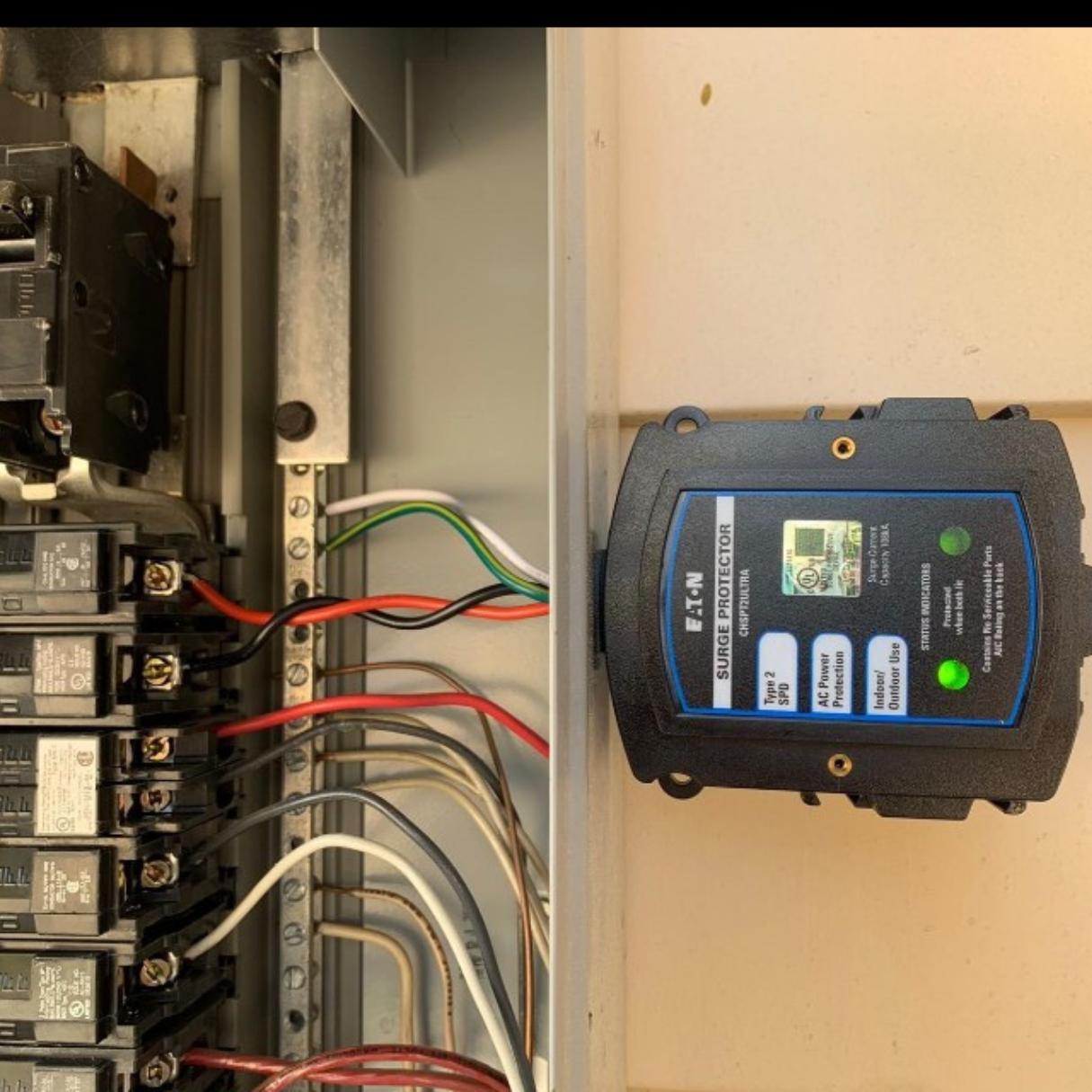
Whole house surge protectors are advanced devices designed to safeguard your entire home from power surges. Unlike individual surge protectors that you plug into outlets, whole house surge protectors are installed at your main electrical panel. Their primary purpose is to intercept and divert excess voltage away from your home’s wiring. This ensures sensitive electronic devices receive a consistently safe level of power.
The Pros of a Whole House Surge Protector
- Comprehensive Protection: Whole house surge protectors safeguard all appliances and devices connected to your home’s electrical system.
- Increased Device Lifespan: Whole house surge protectors extend the lifespan of electronic devices, reducing the need for costly replacements.
- Ease of Installation: Professional electricians can install whole house surge protectors directly into the main electrical panel fairly easily.
- Fire Prevention: Whole house surge protectors contribute to fire prevention by mitigating the potential for electrical overloads that could lead to fires.
- Insurance Benefits: Some insurance providers may offer premium discounts to homeowners who install whole house surge protectors, recognizing the reduced risk of electrical damage.
- Appliance Compatibility: Whole house surge protectors are compatible with all appliances and devices connected to your home’s electrical system, ensuring consistent protection throughout the house.
The Cons of Whole House Surge Protector
- Initial Cost: Whole house surge protectors have a higher upfront cost compared to individual surge protectors. However, this cost may be offset by the comprehensive protection they offer.
- Professional Installation: Installation of whole house surge protectors typically requires a licensed electrician, adding to the overall cost. Attempting DIY installation without the necessary expertise can lead to safety hazards and ineffective protection.
- Limited Protection from External Sources: While whole house surge protectors are effective against internal surges originating from within the home, they may provide limited protection against extremely powerful external sources, such as a direct lightning strike.
- Maintenance and Replacement: Surge protectors, like any electrical device, may require periodic maintenance or replacement to ensure optimal performance. This can result in additional costs over time.
- Not a Guarantee Against All Surges: While whole house surge protectors significantly reduce the risk of damage from power surges, they cannot guarantee absolute protection against all types of surges or catastrophic events.
- Compatibility with Older Wiring: In some cases, homes with outdated or incompatible wiring may face challenges in integrating whole house surge protectors. Upgrading the wiring may be necessary for optimal functionality.
- Limited Effectiveness in Certain Scenarios: In extremely severe cases, such as a direct lightning strike on the power lines, whole house surge protectors may not provide complete protection. However, they can still offer a substantial level of defense in many situations.
Conclusion
Before investing in a whole house surge protector, it’s essential to weigh these pros and cons based on your specific needs, budget, and the electrical characteristics of your home. Consulting with a professional electrician can help determine the most suitable surge protection solution for your circumstances.