Often people have difficulty installing a replacement drive that we send out, and normally it just takes the troubleshooting tips from the manual to get them up and running. However, the manual isn’t always the easiest to find or sort through, so below we’re posting the Siemens Micromaster 420 Troubleshooting section from the manual which should help anyone who is working to get the issues with their drive sorted out.
MRO Electric supplies and repairs Micromaster 420 Drives. To request a quote for a repair or spare, please call 800-691-8511 or email sales@mroelectric.com.
Troubleshooting with the BOP
Warnings and faults displayed on the BOP with Axxx and Fxxx respectively. The individual messages are shown in the Parameter list.
If the motor fails to start when the ON command has been given
– Check that P0010 = 0
– Check that a valid ON signal is present
– Check that P0700 = 2 (for digital input control) or P0700 = 1 (for BOP control)
– Check that the setpoint is present (0 to 10V on Terminal 3) or the setpoint has been entered into the correct parameter, depending on the setpoint source (P1000). Se the Parameter List for further details.
If the motor fails to run after changing the parameters, set P0010 = 30 then P0970 = 1 and press P to reset the inverter to the factory default parameter values.
Now use a switch between terminals 5 and 8 on the control board. The drive should now run to the defined setpoint by analogue input.
Fault Messages
In the event of a failure, the inverter switches off and a fault code appears on the display.
NOTE
To reset the fault code, one of three methods listed below can be used:
1. Cycle the power to the drive.
2. Press the button on the BOP or AOP.
3. Via Digital Input 3 (default setting)
Fault messages are stored in parameter r0947 under their code number (e.g. F0003 = 3). The associated error value is found in parameter r0949. The value 0 is entered if a fault has no error value. It is furthermore possible to read out the point in time that a fault occurred (r0948) and the number of fault messages (P0952) stored in Parameter r0947.
A detailed description of the fault messages is provided in the parameter list.
Alarm Messages
Alarm messages are stored in parameter r2110 under their code number (e.g. A0503 = 503) and can be read out from there. A detailed description of the alarm messages is provided in the parameter list.
Suppressing Fault/Alarm Messages
From the perspective of the application and user, fault-free operation is the decisive criterion when it comes to the acceptance of drive systems. For special applications, not only this, but fault-free operation is required even if an overload condition exists or external events cause faults. For applications such as these (e.g. mixer systems), fault-free operation has a higher priority than the protection of the drive system.
With MICROMASTER, it is possible to suppress up to 3 fault / alarm messages using the indexed parameters P2100 and P2101. The fault / alarm messages to be suppressed (refer to Section “Fault / alarm messages”) are selected using parameter P2100 while the response is entered using parameter P2101. Indices 0 – 2 of the two parameters are used to correlate between suppressing the fault / alarm messages and the response. The following settings are possible for the responses:
0 No response, no display
1 OFF1 stop response
2 OFF2 stop response
3 OFF3 stop response
4 No response, only a warning
Example: Alarm A0911 indicates that the drive has extended the ramp run-down time in order to avoid an overvoltage condition. If you wish to suppress this message, then set the following parameters: P2100[0] = 911 (selects Alarm A0911) P2101[0] = 0 (no response, no display)
NOTE All of the fault messages are assigned the standard response to OFF2 (refer to the fault/alarm list). The standard responses of several fault messages, caused by the hardware – e.g. overcurrent F0001 – can neither be suppressed nor modified.
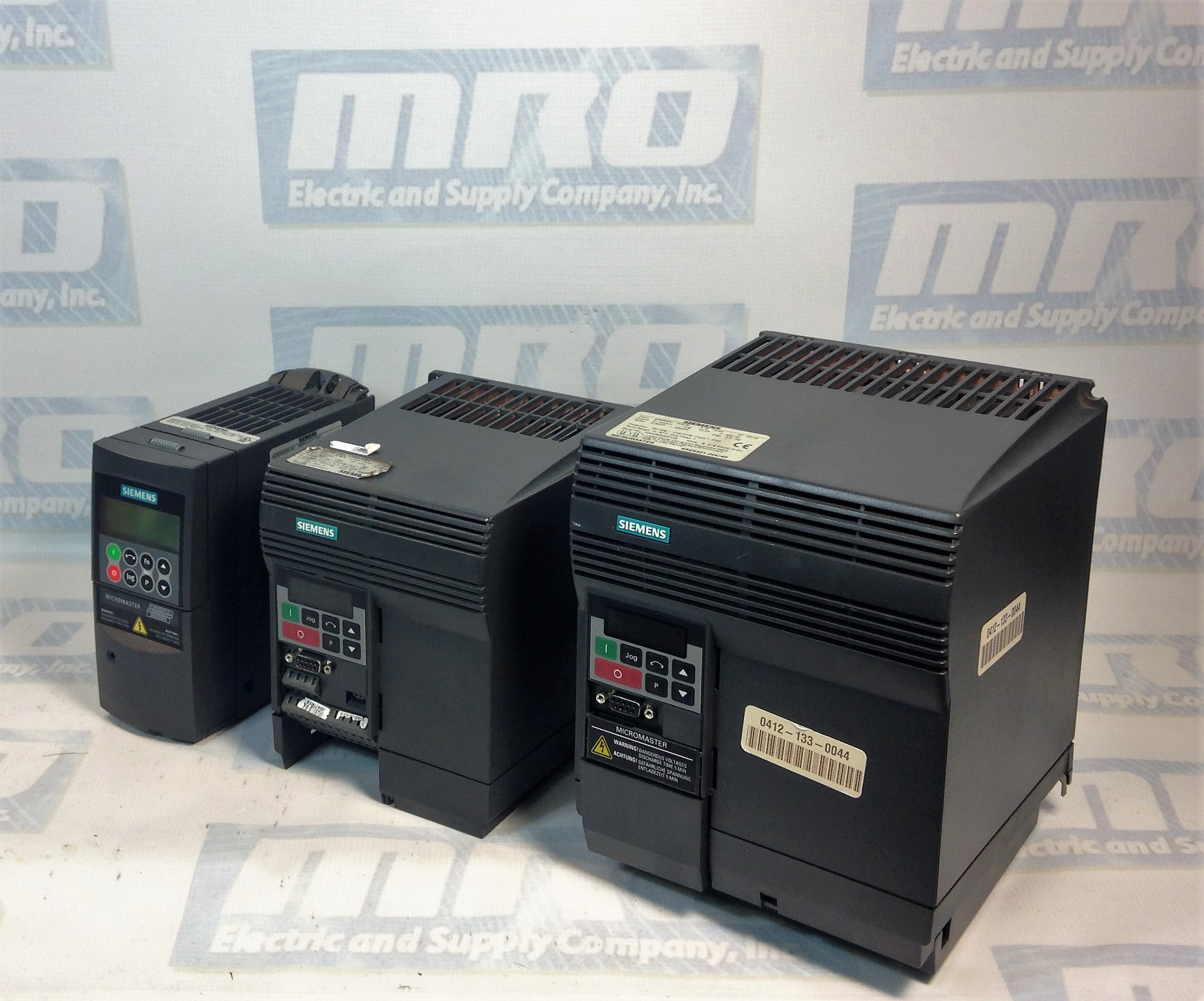
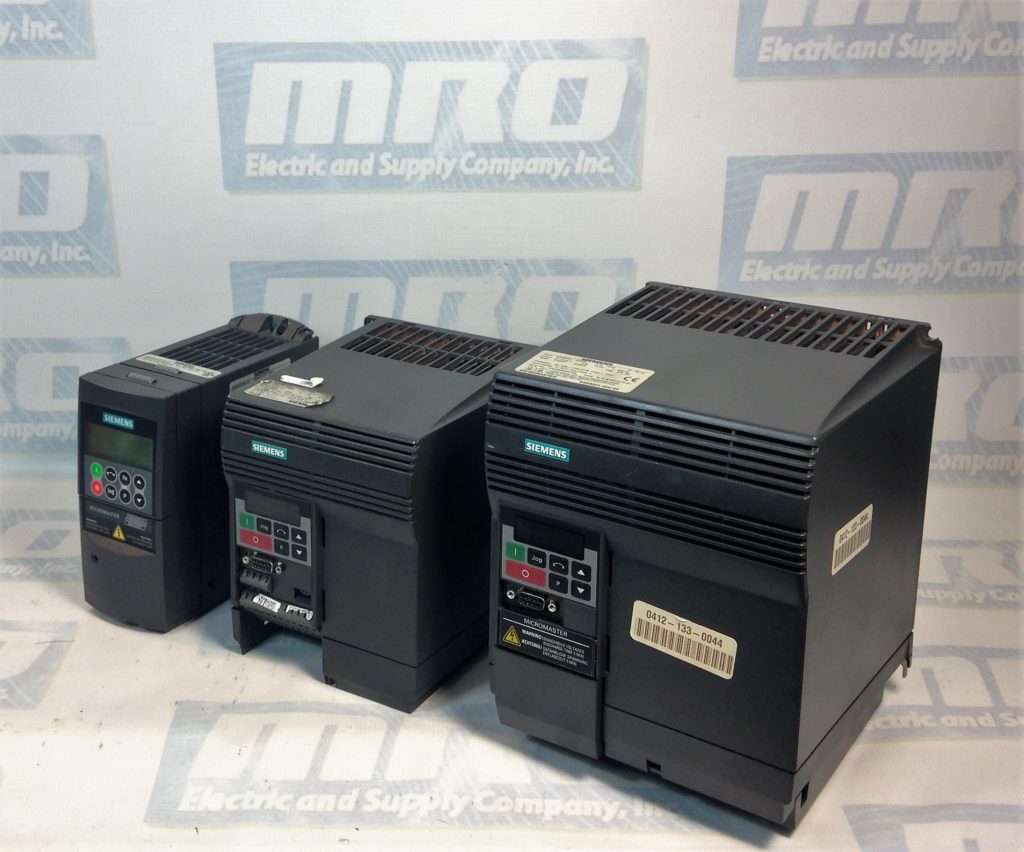
Updated on June 26, 2019 by Ryan Dickinson
Siemens Micromaster 420 fault code f003
Tengo un Micromaster 420. Al encenderlo, luego de una parada de 1 año, el display solo muestra (——).
Me podrían indicar a que nivel puede estar el problema?
Gracias
I have a problem with a micromasterter 420 that smudges these marks on the screen (- – – – -)
vfd gets run command runs to 60 hz right back to 0 hz keeps cycling this 9 volt applied to o 10v
screen showing low battery may not start, battery has been replaced, how do you reset to allow belt to run.