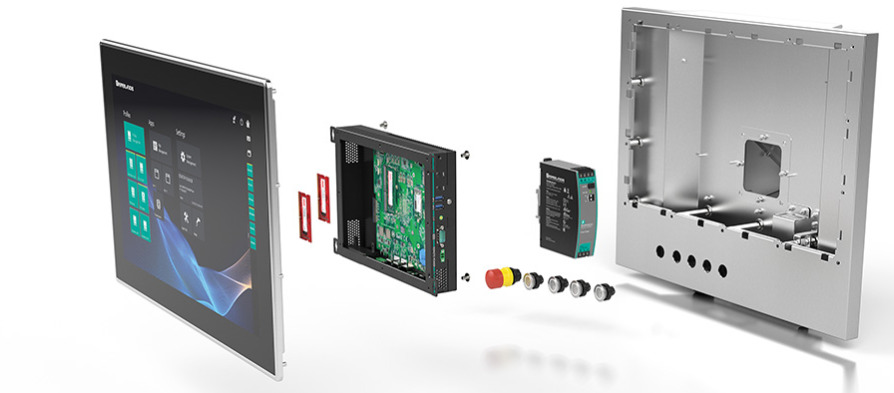
Introduction
With the evolution of technology becoming more sophissticated stresses the importance of faster and more efficient communication. In the early days of machinery, the way humans interacted with equipment would be with pullies and levers. While this system made labor easier, it still required a lot of physical involvement and manpower. Also because workers had communicate manually, orders on each level took a while to convey. As manufacturing and industrial processes advanced, there was more progression in the way humans and machines interacted.
In a previous article, we discussed the Second Industrial Revolution which was characterized by the expansion of electricity. The modern concept of automation begins around this time. Hefty ropes, pullies, and levers eventually became surpassed by switches and buttons. No longer did a team of workers pull heavy chains to raise and lower heavy objects. The use of electricity meant that motorized pulleys and wenches could replace these tasks with a push of a button. This development also meant faster response times in between processes, therefore resulting in faster production times.
While this by far made production in factories a lot faster and more efficient. The need to be more streamlined meant factories still needed to up the game on productivity. This is where the HMI enters the story.
A Brief History
In the Beginning
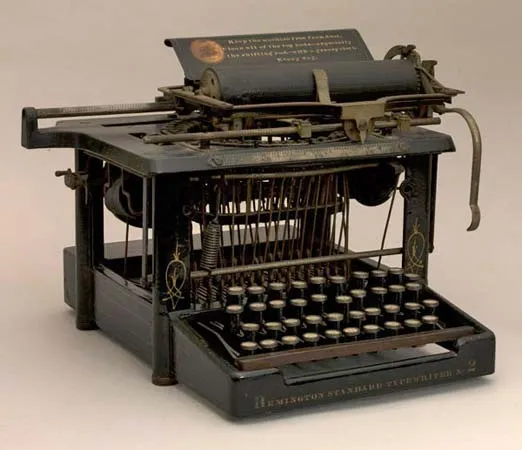
While we are hard pressed to find one today, the earliest HMI can be traced back to the typewriter. Invented in the 1860s, the device provided a tangible connection between human input and machine output. While the typewriter is considered rudimentary by today’s standards. A person able to punch keys and output the information onto paper marked a milestone in machine interfacing. However, the biggest progress for HMI technology comes about during the 20th century.
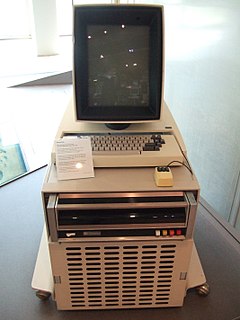
The 20th Century
The mid-20th century saw the rise of computers. Unlike the typewriter, these powerful machines and their interfaces evolved from punch cards to command-line interfaces. This later would progress to graphical user interfaces (GUIs). By 1965 the Royal Radar Establishment developed the first touch screen. Popularized by Xerox PARC’s Alto computer in the 1970s, the GUI allowed users to interact with computers through visual representations such as icons, windows, and menus. Ths technology saw niche use in industries like air traffic control. However, it wasn’t until the 1980s that it gained widespread recognition. Two prominent examples of devices being the Hewlett-Packard HP-150 and the Atari 520ST. Touchscreens revolutionized the way users interacted with machines, providing a more intuitive and direct method of input. Another significant advancement in HMI was the introduction of voice recognition systems.
HMI in the Digital Age
Recent years have witnessed the rise of virtual and augmented reality as emerging interfaces. Virtual reality (VR) and augmented reality (AR) technologies have gained significant traction. VR immerses users in computer-generated environments, while AR overlays digital information onto the real world. These immersive technologies are opening up new possibilities with training and the way operators interact with equipment.
What is HMI?
In the world of industrial automation, Human-machine interface (HMI) plays a crucial role in completing tasks. It enables effective communication and interaction between humans and machines in manufacturing and industrial settings. HMIs serve as the primary interface through which operators monitor and control industrial processes. These interfaces provide real-time data visualization, alarms, and controls that allow operators to make informed decisions and respond quickly to changing conditions. They typically consist of touchscreens, graphical displays, and input devices such as keyboards or keypads. HMIs are used to manage a wide range of industrial automation systems, including robotic assembly lines, control panels, and supervisory control and data acquisition (SCADA) systems.

The use of HMIs in industrial automation has greatly enhanced productivity, efficiency, and safety in manufacturing environments. HMIs in minimize human error and help with downtime. They allow operators to visualize critical information, receive real-time alerts, and respond promptly to abnormal conditions. HMI’s provide clear and concise displays, making it easier for operators to interpret data and make informed decisions. Furthermore, HMIs implement preventive maintenance strategies by providing insights into equipment performance and condition monitoring. By integrating advanced functionalities like data analytics and predictive maintenance, HMIs contribute to proactive approaches in industrial automation.
Conclusion
As industry continues to evolve we already seeing the integration of VR and voice commands in HMI technology. At this point the questions is not so much about “Can we do it?” but rather how streamlined and cost efficient can they be? Only time can tell.
Updated on June 8, 2023 by Ken Cheng