cause personal injury or destroy the motor
Category: Manufacturers
Timeline, CPUs and Programming of the Modicon PLC Series
The Modicon PLC Series has been around for almost 40 years at this point, from the 484 series to the M340 series. The timeline below lists the CPU part numbers, the years they were sold, and what they are programmed with. For more info you can visit our series page here or email sales@mroelectric.com.
Modicon 484
CPU Part Number: AS-C484-xxx
Actively Sold: 1977-1983
Programmed With: P190 programmer
Modicon 584
CPU Part Number: AS-584A-xxx, AS-584M-xxx, AS-584L-xxx
Actively Sold: 1979-1984
Programmed With: Modsoft, ProWorx Plus/Nxt/32 Software
Modicon 984 Chassis Mount
CPU Part Number: P1-984X-008, Px-984A-xxx, Px-984B-xxx
Actively Sold: 1985-1999
Programmed With: ProWorx Plus/Nxt/32 and Modsoft Software
Modicon 984 Slot Mount
CPU Part Number: PC-A984-3xx, PC-D984-xxx, PC-K984-xxx
Actively Sold: 1987-2006
Programmed With: ProWorx Plus/Nxt/32 and Modsoft Software
Modicon Compact 984
CPU Part Number: PC-A984-xxx, PC-E984-2xx
Actively Sold: 1991-2007
Programmed With: Modsoft, ProWorx Plus/Nxt/32, Concept software
Modicon Micro
CPU Part Number: 110CPU311xx, 110CPU411xx, 110CPU512xx, 110CPU612xx
Actively Sold: 1996-2006
Programmed With: Modsoft, ProWorx Plus/Nxt/32 software
Modicon Quantum
CPU Part Number: 140CPUxxxxx
Actively Sold: 1994 to present
Programmed With: ProWorx 32, Concept, Unity software
Modicon Premium
CPU Part Number: TPCX57xxxx, TSXP57xxxx
Actively Sold: 1998 to present
Programmed With: PL7 or Unity software
Modicon Momentum
CPU Part Number: 171CCC7xxxx, 171CCS7xxxx, 171CCC9xxxx
Actively Sold: 1998 to present
Programmed With: ProWorx, Concept software
Modicon M340
CPU Part Number: BMXP341000, BMXP342010, BMXP342020, BMX342030
Actively Sold: 2007 to present
Programmed With: Unity V3.0 software
Unidrive Security Code Basics
For some new User’s of Unidrives, the parameter security system is sometimes found to be a rather mysterious subject. This article will attempt to unveil those mysteries with some help to explain the Control Techniques Unidrive Security Code Basics.
Security Basics
Without entering the basic security code, 149, you will only be able to view Menu 0 parameters. The “as shipped” security code for the Unidrive is 149. To enter this code you would maneuver to #00.00 and enter 149. Once this security code is entered, you will be able to maneuver throughout the Unidrive menu structure freely to view parameters.
After a security code is entered, it will remain in effect until power is removed from the drive or if you wish to re-establish this security, you can set #XX.00 to 2000. (where XX means “any menu” )
The User Security Code parameter is #11.30. The “as shipped” value in this parameter is 149.
For more info you can check our webpage here, or email sales@mroelectric.com or call 1-800-691-8511.
If you find that you cannot change R/W (Read/Write) parameters (including those in Menu 0), someone has most likely assigned their own security code.
User Security Code Assignment
User’s can assign their own 3 digit security code within the range of 1-255 by placing it into #11.30 (writing over the 149) and performing a STORE.1 Note that this does not eliminate or change the “Normal security” code number – 149.
From this point forth, access to parameters will require that code to be placed into #XX.00. At this point you only have access to Menu O. After this code is entered, you must still enter the normal access code (149) to gain access beyond Menu 0 parameters ( full access).
These security methods do not affect serial communications. Security affects only access to parameters through the keypad on the front of the Drive.
Forgotten Security Codes
People often forget their security codes. A User assigned security code is not visible at #11.30 via the serial port (you would still see 149). To retrieve the forgotten security code, you must go in through the “back door” .
“The Back Door”
To obtain the forgotten security code, you can DEPRESS and HOLD the MODE key, LEFT ARROW key and either UP or DOWN Arrow key then APPLY POWER to the drive. The User security code number should appear on the data display at #00.00. Normally, the drive displays the contents of parameter #0.10 upon application of power therefore the User security code may not immediately appear. You must use maneuver to #00.00 to see the forgotten security code then enter it (hit the mode button twice).
Security Bypass
During initial start-up of the drive, having to enter the security code after each power-up can become a nuisance and slow down the start-up process. To bypass or eliminate the need to enter a security code, one can accomplish this by placing a 0 into parameter #11.30 and performing a Store.
If this bypass is done to speed up the start-up process, you should remember to re-assign the 149 default to #11.30 (and Store) before leaving the job site. Otherwise, the drive will have no parameter access security.
Note: Defaulting the drive parameters (using 1244 or 1254) does not reset the User security code. A previously assigned code by the User will remain in effect even after defaulting parameters.
Additional information
Parameter 0.49 Security Status
Coding: RO, U Range: 0 to 1000
This parameter indicates the current status of the drive parameter security system. Each digit indicates a particular aspect of security as follows:-
Units digit: 0 = Standard security has been unlocked 1 = Standard security is still set
Tens digit: 0 = User security has been unlocked or is not active 1 = User security is active preventing RW access
Hundreds digit: 1 = Parameter 11.30 not equal to 149*
Thousands digit: 1 = Parameter 11.30 equal to zero*
* The value of 11.30 is the last value written by the user. Parameter 11.30 always appears as 149 when first accessed by the keypad to hide the real value last written by the user. If 11.30=149 then user security is cleared. If 11.30=0 then user security and security preventing access outside menu 0 is cleared.
Note: – In contrast to all the other parameters in menu 0, this parameter does not exist in any other menu.
The Modicon 984 Family of PLCs
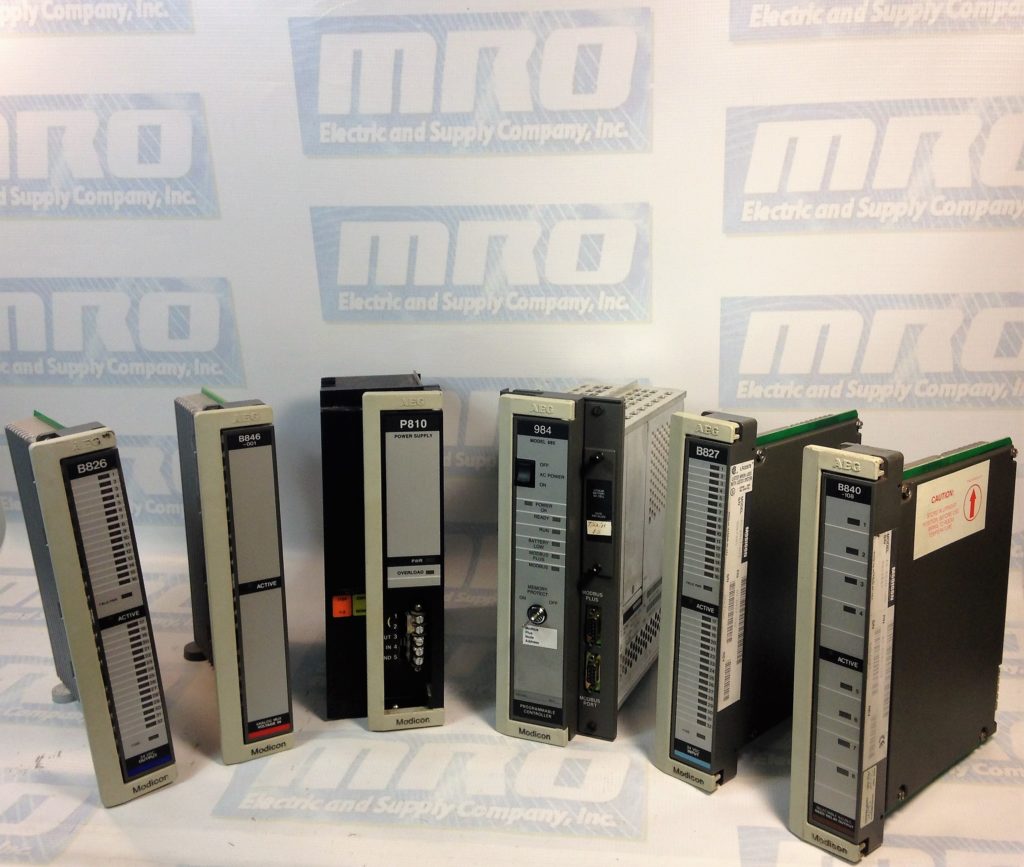
Micromaster Frequency Inverter for Drive Technology
Siemens Micromaster Frequency Inverter drives are used everywhere in the manufacturing and process industry. Specifically, they are used for outputs ranging from 0.12 kW to 250 kW in the manufacturing industry, and normally in applications ranging from pumps to extruders to winding machine to conveyor systems.
The Micromaster series has a compact design which allows it to work perfectly for cabinet mounting and integration into the design of both stand-alone and series machines. They enable maximum utilization of the available mounting surface, from small outputs to large outputs, with a wide range of supply voltages. This is the reason that the Micromaster drives cover a wide field of applications. The options concept also opens up additional possibilities for customization of each drive. Different communication module allow for use in common network applications, plain text panels simplify operation, and additional base components such as reactors complement the compact solution.
The Micromaster series is made up of three groups that each have unique strengths. The Micromaster 420 drives are universal usage, the Micromaster 430 drives are specialized for pumps and fans, and the Micromaster 440 drives all all around workhorses.
If you have more questions about ordering you can email sales@mroelectric.com or call 1-800-691-8511. You can also visit the Micromaster series page here.
Simodrive 611 Productivity Info
The Simodrive 611 series is meant to be a converter system that is suitable for drive assemblies that can be combines with each other to enable fast and flexible synchronization of the drive performance. This will work for a number of axes on the machine and sets the Simodrive 611 productivity levels.
Siemens Micromaster 430 Series Info
The Siemens Micromaster 430 series is a drive system that was designed to perform a set of specific requirements. There has been a demand for inverter solutions that can be flexibly in simply adapted to solve a broad variety of challenges This type of flexibility is the main characteristic of the Siemens Micromaster 430 series and one of the main reasons for the widespread use of these drives.