Servo motors are the unsung heroes of the modern technological landscape, silently powering everything from robots and drones to 3D printers and CNC machines. These miniature marvels are responsible for precise control and motion, making them indispensable in various industries. In this comprehensive guide, we’ll demystify the magic behind servo motors, explaining their operation, applications, and the intricate engineering that allows them to work their wonders.
Introduction to Servo Motors
At first glance, a servo motor may appear to be a simple, compact device. Still, beneath its unassuming exterior lies a sophisticated piece of engineering that combines precision, feedback control systems, and electrical circuits to deliver highly accurate rotational motion.
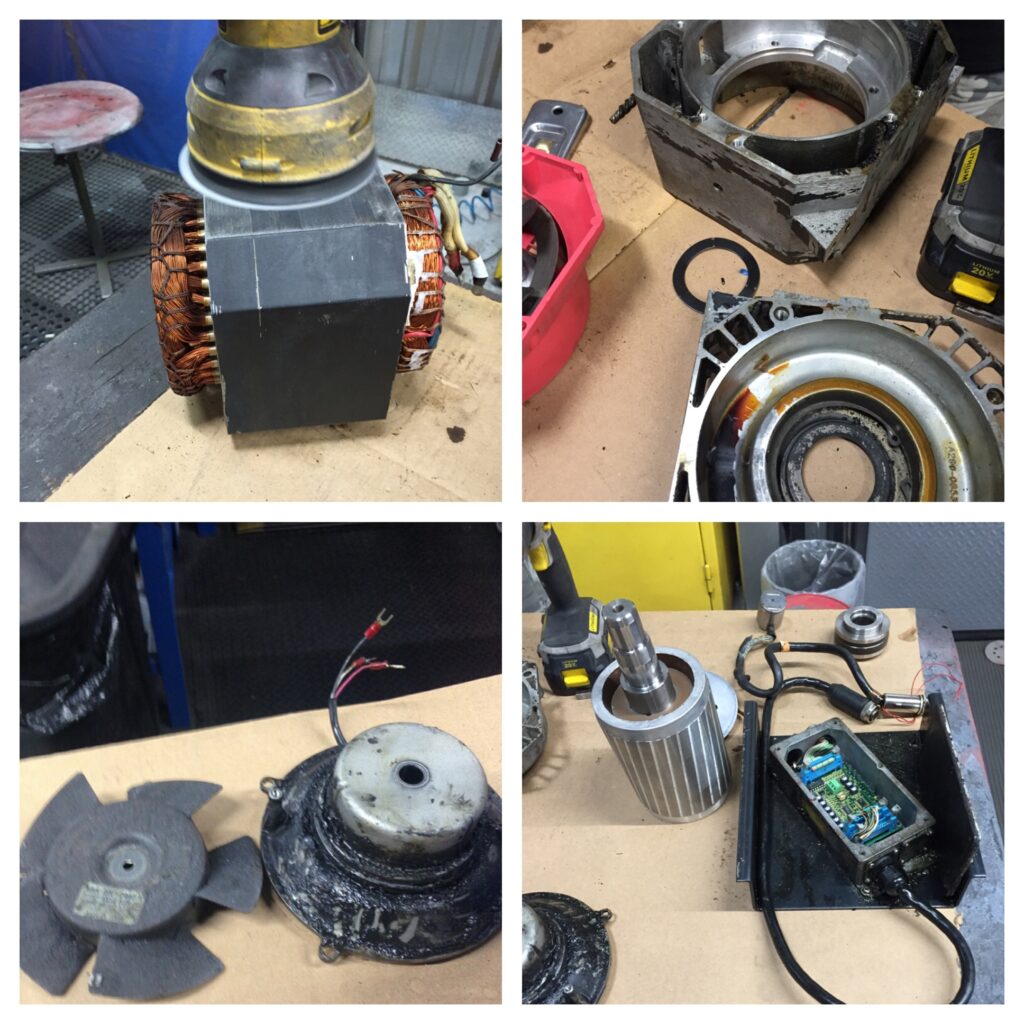
A servo motor typically consists of four main components:
- Motor: The heart of the servo, this component generates mechanical motion when electricity is applied.
- Feedback system: A sensor (usually a potentiometer or an encoder) that continuously monitors the motor’s position, allowing for real-time adjustments.
- Control circuit: The brain of the servo, responsible for processing feedback data and determining the required motor movement.
- Output shaft: This shaft extends from the motor and connects to the equipment or mechanism that requires precise motion.
Now, let’s dive into the inner workings of servo motors.
Basic Working Principle
Servo motors operate on a closed-loop control system, meaning they continuously receive feedback about their position and adjust accordingly. This feedback loop is the core concept behind their precision.
Here’s a simplified breakdown of how a servo motor works:
- Reference Input: You set a desired position for the servo motor using a control signal, typically in the form of a pulse-width modulation (PWM) signal. The width of the pulse determines the target position.
- Feedback Mechanism: The servo motor’s feedback system continuously monitors its current position, often using a potentiometer or an encoder. This feedback information is sent to the control circuit.
- Error Calculation: The control circuit calculates the difference (error) between the desired position and the actual position, as reported by the feedback mechanism.
- Amplification and Amplifier: The error signal is amplified to provide sufficient power to the motor. This amplified error signal drives the motor to move in the direction that reduces the error.
- Motor Movement: The motor responds to the amplified error signal and begins to move the output shaft toward the desired position.
- Feedback Loop: As the motor moves, the feedback system continues to monitor the position. The control circuit makes constant adjustments to minimize the error, ensuring that the motor reaches and maintains the desired position.
- Stabilization: Once the motor reaches the desired position, the control circuit stabilizes it by reducing the error to zero. The motor then holds the position until new input is received.
This closed-loop control system is what distinguishes servo motors from standard DC motors. The continuous feedback and adjustment process result in precise, smooth, and reliable motion control.
The Role of Feedback Systems
To grasp the importance of feedback systems in servo motors, it’s essential to understand the two primary types: potentiometers and encoders.
1. Potentiometers
Potentiometers, or pots for short, are variable resistors that produce an electrical output based on the position of a mechanical shaft. In servo motors, a potentiometer is mechanically linked to the motor’s output shaft. As the shaft rotates, the potentiometer’s resistance changes, producing a voltage signal proportional to the shaft’s position.
While potentiometers are cost-effective and straightforward, they may not provide the level of precision required in some applications due to wear and tear over time.
2. Encoders
Encoders are highly accurate sensors that provide digital feedback about the motor’s position. They come in two main types: incremental encoders and absolute encoders.
a. Incremental Encoders
Incremental encoders produce a series of pulses as the motor shaft rotates. These pulses are used to measure the direction and distance of rotation. By counting the pulses, the control circuit can determine the shaft’s position accurately.
Incremental encoders are reliable but lack the ability to report the absolute position of the shaft when powered up, requiring a reference point to initialize the position.
b. Absolute Encoders
Absolute encoders provide a unique digital code for every possible position of the motor shaft. This code represents the shaft’s absolute position, eliminating the need for homing or referencing when the system is powered up.
Absolute encoders offer unparalleled precision and are ideal for applications that require precise positioning, such as robotic arms and CNC machines.
The choice between potentiometers and encoders depends on the specific requirements of the application. While potentiometers are suitable for simpler and cost-sensitive projects, encoders are preferred for high-precision and critical tasks.
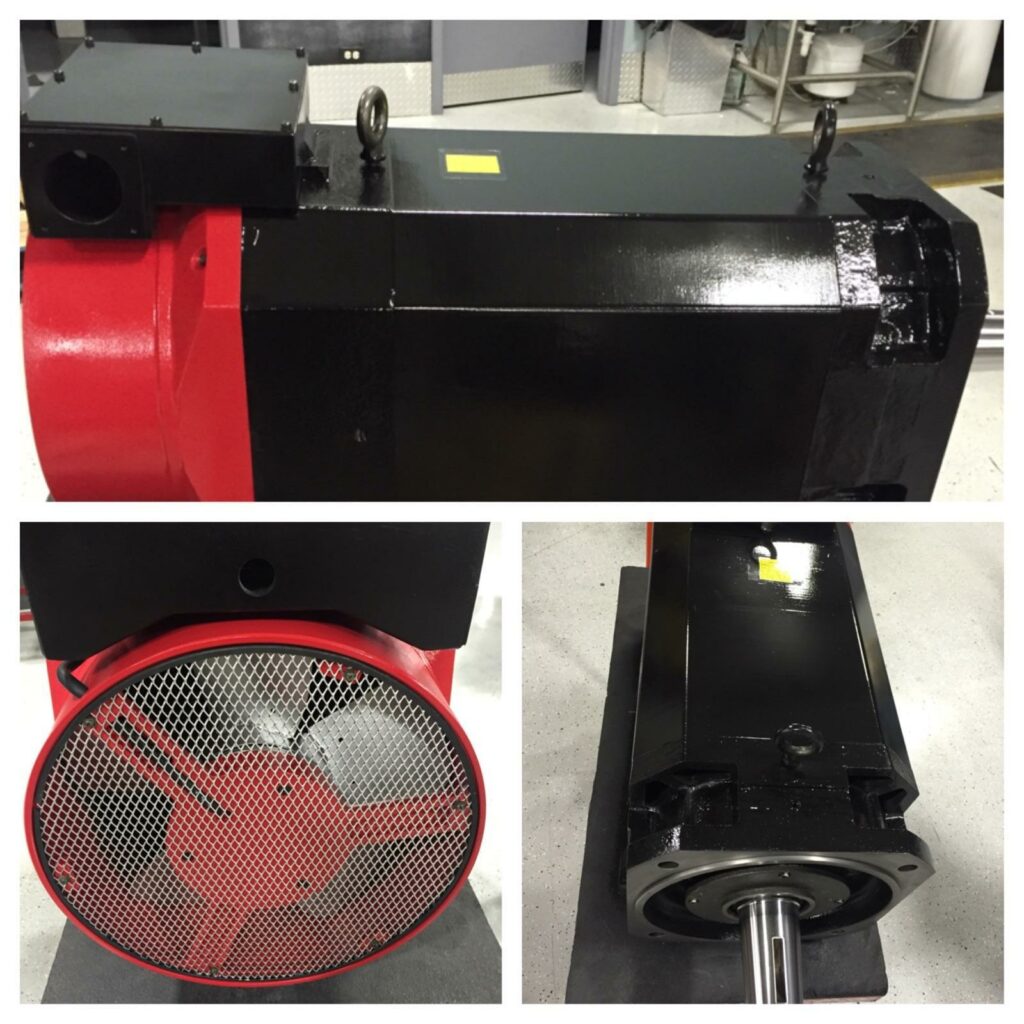
Types of Servo Motors
Servo motors come in various types, each designed for specific applications and performance characteristics. The primary types of servo motors include:
1. DC Servo Motors
DC servo motors are the most common type and are well-suited for applications that require high torque and speed control. They are relatively simple and cost-effective, making them popular in industries like robotics and automation.
2. AC Servo Motors
AC servo motors are known for their high power density and efficiency. They are commonly used in industrial machinery and applications that require precise and rapid positioning.
3. Brushless DC Servo Motors
Brushless DC servo motors offer the advantages of both DC and AC servo motors. They provide high efficiency, low maintenance, and excellent torque control, making them suitable for applications like aerospace and medical devices.
4. Linear Servo Motors
Linear servo motors are designed for linear motion instead of rotational motion. They are used in applications like CNC machines, 3D printers, and automated conveyor systems.
5. Servo Stepper Motors
Servo stepper motors combine the features of servo and stepper motors. They provide precise motion control and high torque at low speeds, making them ideal for applications such as CNC machining and camera positioning.
Applications of Servo Motors
Servo motors find applications across a wide range of industries due to their precision and reliability. Here are some notable examples:
1. Robotics
Servo motors are the backbone of robotic systems, enabling precise control of robot arms, grippers, and joints. They are used in industrial robots for tasks like welding, painting, and material handling, as well as in consumer robots like vacuum cleaners and drones.
2. CNC Machining
Computer Numerical Control (CNC) machines rely on servo motors to move the cutting tools with high accuracy. CNC milling machines, lathes, and routers use servo motors for positioning and controlling the cutting process.
3. Aerospace
In the aerospace industry, servo motors are crucial for controlling flight surfaces such as ailerons, elevators, and rudders. They are also used in landing gear systems and satellite positioning.
4. Medical Devices
Precision is paramount in medical devices, and servo motors play a vital role in equipment like robotic surgical systems, MRI machines, and automated drug delivery systems.
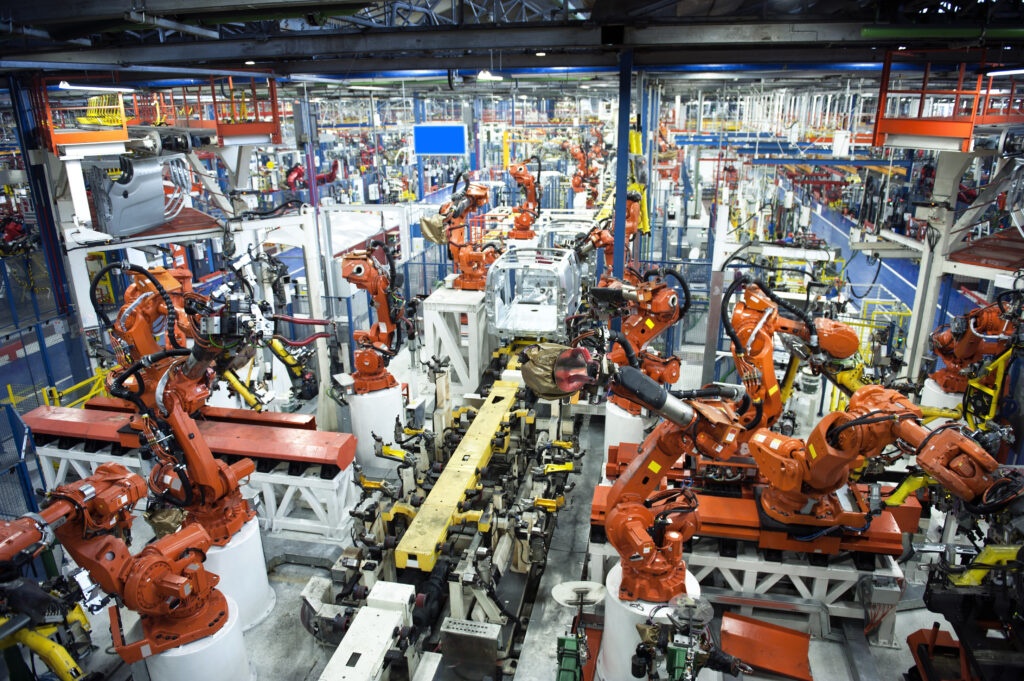
5. Automotive
Servo motors are used in various automotive applications, including electronic power steering systems, throttle control, and engine management systems. Electric vehicles (EVs) also rely on servo motors for precise control of motor functions.
6. Industrial Automation
In manufacturing and industrial automation, servo motors are used in conveyor systems, packaging machinery, and material handling equipment. They enable precise control and synchronization of production processes.
7. Consumer Electronics
Servo motors are found in everyday consumer electronics like digital cameras, camcorders, and disk drives, where they enable smooth and accurate movements.
Advantages of Servo Motors
Servo motors offer several advantages that make them the preferred choice in various applications:
1. High Precision: Servo motors provide exceptional accuracy and repeatability, making them ideal for tasks that require precise positioning.
2. Rapid Response: These motors can respond to changes in input commands quickly, ensuring rapid adjustments and real-time control.
3. High Torque at Low Speeds: Servo motors can deliver substantial torque even at low speeds, making them suitable for applications requiring both power and finesse.
4. Closed-Loop Control: The feedback loop in servo systems ensures that the motor always moves to the desired position, even when external factors like load or temperature change.
5. Energy Efficiency: Servo motors are energy-efficient, as they only consume power when in motion and can hold a stable position with minimal energy usage.
6. Low Maintenance: Brushless servo motors, in particular, have fewer moving parts, reducing the need for maintenance and increasing their lifespan.
Challenges and Limitations
While servo motors are incredibly versatile and powerful, they do have some limitations and challenges to consider:
1. Cost: High-precision servo systems can be expensive, making them less suitable for budget-conscious projects.
2. Complexity: Setting up and tuning a servo system can be complex, requiring expertise in control theory and electronics.
3. Heat Generation: Servo motors can generate heat during operation, which may necessitate cooling mechanisms in some applications.
4. Power Consumption: Continuous feedback and control require power, which can be a concern in battery-powered applications.
5. Noise and Vibration: Some servo motors may produce audible noise and vibrations, which could be undesirable in certain settings.
Conclusion
Servo motors are the unsung heroes of precision motion control, enabling countless technological advancements across various industries. Their ability to provide high precision, rapid response, and closed-loop control makes them invaluable in applications ranging from robotics and aerospace to medical devices and consumer electronics.
Understanding how servo motors work, the role of feedback systems, and the different types available empowers engineers and enthusiasts to harness their potential effectively. While they come with challenges and limitations, the benefits they offer in terms of accuracy, control, and efficiency make them an essential component in the world of automation and robotics. As technology continues to evolve, so will the capabilities of servo motors, driving innovation and pushing the boundaries of what’s possible in the world of precise motion control.
Thanks for sharing the information about servo motors, it helps me a lot.