Industrial automation has undergone a remarkable transformation over the decades, and at the heart of this evolution lies the Programmable Logic Controller, or PLC. In this comprehensive exploration, we will delve into the fascinating history of PLCs in industrial automation. From their humble beginnings as relay-based control systems to their current status as sophisticated digital control units, we will trace the journey of PLCs through the years, highlighting key milestones, technological advancements, and the profound impact they’ve had on modern industry.
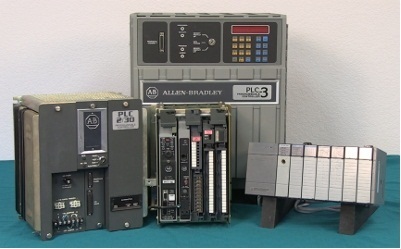
Chapter 1: The Birth of PLCs
The concept of automation in industrial processes can be traced back to the early 20th century when factories sought ways to improve efficiency and reduce human error. Before PLCs, control systems relied on cumbersome and limited relay logic. It was not until the late 1960s that the first true PLC emerged.
In 1968, a team at Bedford Associates, led by engineer Dick Morley, developed the first PLC, known as the “084.” This revolutionary device aimed to replace traditional hardwired relay systems with a digital alternative. The 084 was a significant departure from earlier control mechanisms, introducing the concept of programming controllers through software, marking a turning point in industrial automation.
Chapter 2: PLCs in the 20th Century
Throughout the 20th century, PLCs underwent significant advancements and refinements. Microprocessor technology, which was rapidly evolving at the time, played a pivotal role in the development of PLCs.
The 1970s saw the emergence of major PLC manufacturers, including Allen-Bradley, Siemens, and Mitsubishi, who introduced their own versions of programmable controllers. These manufacturers began producing PLCs with increased processing power and expanded memory, enabling them to handle more complex tasks and accommodate a broader range of applications.
In the 1980s, PLCs started integrating communication capabilities, such as serial and Ethernet communication. This allowed PLCs to communicate with other devices and systems, paving the way for more extensive automation networks and remote monitoring.
Chapter 3: Modern PLCs
The 21st century brought about a new era of PLC technology. PLCs became even more powerful, versatile, and reliable. Key advancements in modern PLCs include:
- Integration of Communication Protocols: Modern PLCs support a wide array of communication protocols, making it easier to connect with various devices, sensors, and controllers. This seamless integration contributes to the creation of interconnected automation systems.
- Increased Processing Power: PLCs now boast significantly more processing power than their predecessors, allowing for faster execution of complex control algorithms and real-time data processing.
- Enhanced Reliability and Durability: PLCs are designed to withstand harsh industrial environments. They feature rugged construction and redundancy options to ensure continuous operation, even in the face of component failures.
- Human-Machine Interface (HMI): PLCs have evolved to include user-friendly HMIs, providing operators with intuitive interfaces for monitoring and controlling industrial processes.
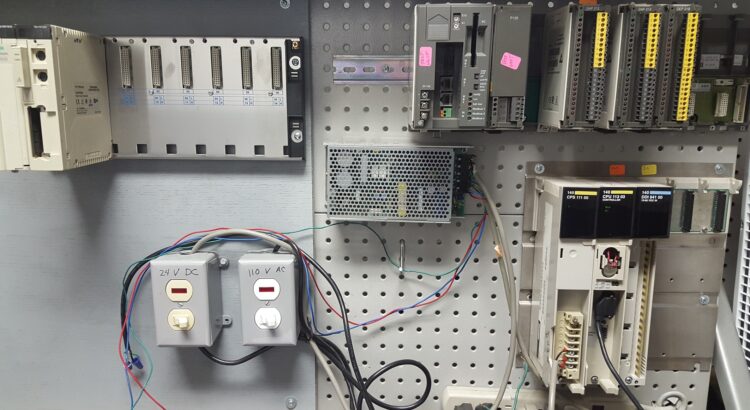
Chapter 4: PLC Applications
PLCs have found applications in various industries, revolutionizing the way processes are controlled and managed. Some notable applications include:
- Manufacturing Automation: PLCs play a pivotal role in manufacturing, controlling assembly lines, robotic arms, and quality control processes. They enable precise control, reduce cycle times, and improve production efficiency.
- Process Control: Industries like chemical manufacturing, petrochemicals, and food processing rely on PLCs to maintain tight control over complex processes, ensuring safety and product quality.
- Building Automation: PLCs manage HVAC systems, lighting, security, and access control in commercial and residential buildings, contributing to energy efficiency and occupant comfort.
- Transportation and Logistics: Conveyor systems, traffic lights, and airport baggage handling systems are efficiently controlled by PLCs, streamlining operations and enhancing safety.
- Energy Management: PLCs are crucial in power generation and distribution, optimizing energy production and ensuring reliable electrical grids.
- Healthcare and Pharmaceuticals: PLCs are used in laboratory automation, pharmaceutical production, and medical device manufacturing to maintain precise control over critical processes.
Chapter 5: Benefits of Using PLCs
The widespread adoption of PLCs is driven by the numerous advantages they offer:
- Improved Efficiency: PLCs provide faster response times, reduced downtime, and enhanced precision, leading to higher production rates and cost savings.
- Enhanced Reliability: PLCs offer redundancy options, fault tolerance mechanisms, and predictive maintenance capabilities, ensuring that critical processes remain operational.
- Cost Savings: PLCs reduce labor costs, improve energy efficiency, and minimize material wastage, resulting in significant financial benefits for industries.
- Scalability: PLCs are highly scalable, allowing for the addition of new components and devices as operations expand or change.
Chapter 6: Challenges and Considerations
While PLCs have revolutionized industrial automation, they also present challenges that must be addressed:
- Cybersecurity Concerns: PLCs are susceptible to cyberattacks, making robust cybersecurity measures a necessity to protect critical infrastructure.
- Training and Skill Development: A skilled workforce is essential for effective PLC programming and maintenance. Continuous training and certification programs are vital to address this challenge.
- Integration with Legacy Systems: Retrofitting older equipment with PLCs can be complex due to compatibility issues. Strategies for smooth integration and data migration are crucial.
Conclusion
The history of PLCs in industrial automation is a testament to human ingenuity and the relentless pursuit of efficiency and precision in manufacturing and other industrial processes. From their humble beginnings as relay-based control systems to their current status as powerful digital control units, PLCs have played a pivotal role in shaping the modern industrial landscape.
As we look ahead, PLCs continue to evolve, embracing technologies like edge computing, IoT integration, artificial intelligence, and cloud-based solutions. These innovations promise to further enhance the capabilities of PLCs, ensuring their relevance and impact in industrial automation for many years to come.