Yaskawa servo drives are at the heart of precision motion control in various industrial applications. They provide the necessary intelligence and power to drive servo motors, ensuring accurate positioning, speed control, and torque management. However, even the most robust systems can encounter issues that disrupt operations. Troubleshooting Yaskawa servo drives requires a systematic approach, a deep understanding of the equipment, and knowledge of common problems and their solutions. In this comprehensive guide, we will explore a wide range of tips and techniques to help you become proficient in diagnosing and resolving issues with Yaskawa servo drives.
Chapter 1: Understanding Yaskawa Servo Drives
1.1 Servo Drive Basics
Before diving into troubleshooting, it’s crucial to have a solid understanding of how Yaskawa servo drives function. Here’s a brief overview:
- Servo drives control the motion of servo motors, regulating position, speed, and torque.
- They receive control signals from a controller (e.g., PLC) and convert them into power output to the motor.
- Feedback devices (encoders or resolvers) provide position and speed information to the drive, allowing it to maintain accuracy.
- Servo drives are equipped with protection features like overcurrent, overvoltage, and overtemperature safeguards.
1.2 Yaskawa Drive Models and Features
Different Yaskawa servo drives come with varying features and capabilities. Understanding the specific model and its features is essential for effective troubleshooting. Key factors to consider include:
- Maximum current and voltage ratings.
- Communication interfaces (e.g., EtherCAT, Ethernet/IP, Mechatrolink).
- Control modes (position control, velocity control, torque control).
- Feedback compatibility and resolution.
- Diagnostic tools and software support.
Chapter 2: Common Issues and Symptoms
2.1 Overheating
Symptoms:
- Drive feels excessively hot to the touch.
- Frequent thermal warnings or shutdowns.
- Degraded performance when the drive gets hot.
Causes and Solutions:
- Inadequate ventilation: Ensure proper airflow around the drive.
- High duty cycle: Reduce the load or use a higher-rated drive.
- Faulty cooling components: Inspect and replace fans or heatsinks as needed.
2.2 Communication Problems
Symptoms:
- Loss of communication between the drive and controller.
- Error messages related to communication errors.
- Inconsistent or erratic behavior of the servo system.
Causes and Solutions:
- Loose or damaged cables: Check and secure all communication cables.
- Incorrect communication settings: Verify and adjust communication parameters.
- Electromagnetic interference: Shield cables and isolate the drive from interference sources.
2.3 Positioning Errors
Symptoms:
- Inaccurate positioning of the servo motor.
- Oscillations or overshooting during movement.
- Unusual noises or vibrations.
Causes and Solutions:
- Feedback device issues: Inspect encoders or resolvers for damage or misalignment.
- PID tuning problems: Adjust the Proportional-Integral-Derivative (PID) control parameters.
- Mechanical issues: Examine the mechanical components for wear or misalignment.
2.4 Fault Codes
Symptoms:
- The drive displays fault codes or alarms.
- Operation halts due to fault detection.
Causes and Solutions:
- Refer to the user manual for fault code explanations.
- Address the specific issue indicated by the fault code (e.g., overcurrent, overvoltage).
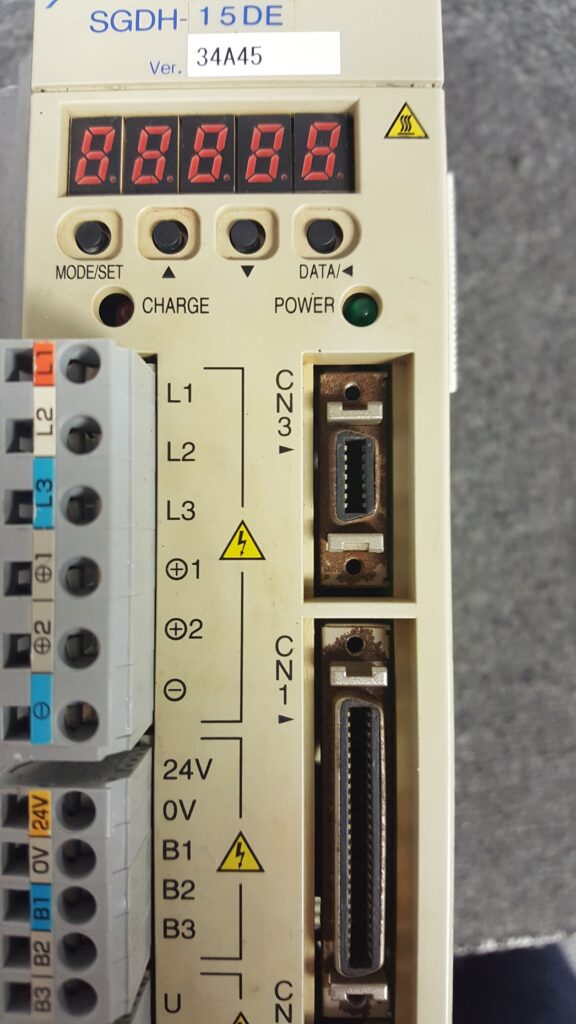
Chapter 3: Troubleshooting Tips
3.1 Visual Inspection
Start troubleshooting with a thorough visual inspection of the servo drive system:
- Check for loose or disconnected cables, damaged wires, or frayed insulation.
- Verify that the grounding is proper and that there are no loose connections.
- Inspect the servo motor and mechanics for physical issues such as misalignment or worn parts.
3.2 Monitor Feedback Signals
Use diagnostic tools to monitor the feedback device’s signals, which are crucial for precise control:
- Ensure that the feedback device (encoder or resolver) is securely connected.
- Verify that the feedback signals are consistent and match the expected values.
- Check for irregularities or noise in the feedback signals using an oscilloscope.
3.3 Review Drive Parameters
Access the drive’s configuration settings using Yaskawa’s software tools:
- Review and validate motor control settings, including torque limits and velocity limits.
- Confirm the feedback device configuration, including encoder type and resolution.
- Adjust PID control parameters (Proportional, Integral, Derivative gains) as needed.
3.4 Analyze Drive Behavior
Observe the drive’s behavior during operation, paying attention to any unusual patterns:
- Note any unexpected movements, oscillations, or excessive noise.
- Use an oscilloscope to analyze electrical signals for abnormalities.
- Monitor temperature levels to check for overheating during operation.
3.5 Check Fault Logs
Yaskawa servo drives often maintain logs of fault history and alarms. Review these logs to identify recurring issues and patterns:
- Identify the root causes of previous faults and address them proactively.
- Clear the fault history in the drive once issues are resolved to prevent confusion.
3.6 Isolate the Load
Disconnect the load from the servo motor and test the drive with a dummy load, if possible:
- Isolating the load helps determine whether the issue is related to the drive itself or the connected machinery.
- Ensure the drive functions correctly with no load before reconnecting the actual load.
Chapter 4: Preventive Maintenance
4.1 Regular Inspections
Implement a preventive maintenance schedule to keep your servo drive system in optimal condition:
- Conduct routine visual inspections for loose connections and cable integrity.
- Clean the drive and surrounding components to prevent dust buildup.
- Lubricate mechanical parts as needed and check for wear.
4.2 Backup Drive Parameters
Before making any changes to drive parameters, create backups of the existing configuration:
- Store backup files securely for quick restoration in case of unintended changes or drive replacements.
- Document parameter changes for future reference.
4.3 Maintain Documentation
Maintain detailed documentation of your servo drive system, including:
- Wiring diagrams and connection layouts.
- Parameter settings and any modifications made.
- Maintenance records, including dates and descriptions of tasks performed.
Chapter 5: Advanced Troubleshooting
5.1 Use Yaskawa Diagnostic Tools
Yaskawa provides diagnostic tools and software that offer advanced troubleshooting capabilities:
- Yaskawa DriveWizard software allows for real-time monitoring and parameter adjustments.
- Yaskawa’s official support resources and technical documentation provide valuable insights.
5.2 Analyze Waveforms
For complex issues, use an oscilloscope to analyze waveforms of control signals, feedback signals, and power outputs:
- Compare observed waveforms with expected patterns to identify discrepancies.
- Look for noise, voltage spikes, or irregularities in the signals.
5.3 Seek Professional Support
If troubleshooting efforts do not lead to a resolution or if the issue requires specialized knowledge, consider seeking professional support:
- Contact Yaskawa’s technical support or a certified service provider for expert guidance.
- Avoid attempting repairs beyond your expertise to prevent further damage.
Conclusion
Troubleshooting Yaskawa servo drives can be a challenging yet rewarding process. It requires a combination of knowledge, patience, and systematic problem-solving techniques. By understanding the basics of servo drives, recognizing common issues and their symptoms, and following the tips and techniques outlined in this guide, you can effectively diagnose and resolve problems, keeping your Yaskawa servo drive systems running smoothly. Remember that preventive maintenance, documentation, and access to diagnostic tools are key elements of successful troubleshooting and long-term reliability in your industrial applications.