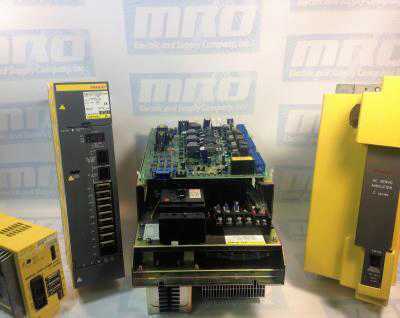
Fanuc Spindle Amp Alarm Codes for Alpha Series
Fanuc Spindle Amp Alarm codes for amplifiers that start with part number A06B-6088, A06B-6102, and A06B-6078.
“A” Program Rom abnormality (Not Installed)
AL-01 Motor Overheat
AL-02 Excessive speed deviation
AL-03 DC Link fuse blown
AL-04 Input fuse blown
AL-05 Control power supply
AL-06 Over Speed
AL-07 Excessive Speed
AL-08 High Input Voltage
AL-09 Excessive load on main circuit section
AL-10 Low input voltage
AL-11 Over-voltage in DC link section
AL-12 Over-current in DC link section
AL-13 CPU Internal data memory abnormality
AL-15 Spindle switch/output switch alarm
AL-16 RAM Abnormality
AL-18 Program ROM checksum error
AL-19 Excessive U phase current detection circuit offset
AL-20 Excessive V phase current detection circuit offset
AL-24 Serial transfer data error
AL-25 Serial transfer data stopped
MRO Electric and Supply maintains a comprehensive stock of new and used FANUC CNC parts including FANUC Spindle Amps. If you need a replacement part, please call 800-691-8511 or email sales@mroelectric.com.
AL-26 Disconnection of speed detection signal for C’s contouring control
AL-27 Position coder signal disconnection
AL-28 Disconnection of position detection signals for C’s contouring control
AL-29 Short-time overload
AL-30 Input circuit over current
AL-31 Speed detection signal disconnection motor restraint alarm
AL-32 Abnormality in RAM internal to LSI for serial data transfer
AL-33 Insufficient DC link section charging
AL-34 Parameter data setting beyond allowable range of values
AL-35 Excessive gear ratio data setting
AL-36 Error counter overflow
AL-37 Speed detector parameter setting error
AL-39 Alarm for indicating failure in detecting 1-rotation signal for C’s contouring control
AL-40 Alarm for indicating 1-rotation signal for C’s contouring control not detected
AL-41 Alarm for indicating failure in detecting position coder 1-rotation signal
AL-42 Alarm for indication position coder 1-rotation not detected
AL-43 Alarm for indicating disconnection of position coder signal for differential speed mode
AL-46 Alarm for indicating failure in detecting position coder 1 rotation signal in thread cutting operation
AL-47 Position coder signal abnormality
AL-48 Position coder 1-rotation signal abnormality
AL-49 The converted differential speed is too high
AL-50 Excessive speed command calculation value in spindle synchronization control
AL-51 Under voltage at DC link section
AL-52 ITP signal abnormality 1
AL-53 ITP signal abnormality 2
AL-54 Overload current alarm
AL-55 Power line abnormality in spindle switching/output switching
AL-56 Cooling fan error.