Variable Frequency Drives (VFDs) have become ubiquitous in the world of industrial automation and energy management. They are remarkable devices that play a crucial role in regulating the speed and efficiency of electric motors. Whether you’re a seasoned engineer or just a curious enthusiast, understanding how VFDs work can empower you with valuable knowledge about the heart of modern manufacturing processes and energy-efficient systems. In this comprehensive guide, we will explore the inner workings of VFDs, from their basic principles to their applications in various industries.
The Basics of VFDs
At its core, a Variable Frequency Drive is an electronic device designed to control the frequency and voltage supplied to an AC (Alternating Current) motor. By altering these two key parameters, VFDs can precisely manipulate the motor’s speed, allowing it to operate at varying speeds with incredible precision. This fundamental capability finds applications across numerous industries, from HVAC (Heating, Ventilation, and Air Conditioning) systems to manufacturing processes, where precise control of motor speed is essential.
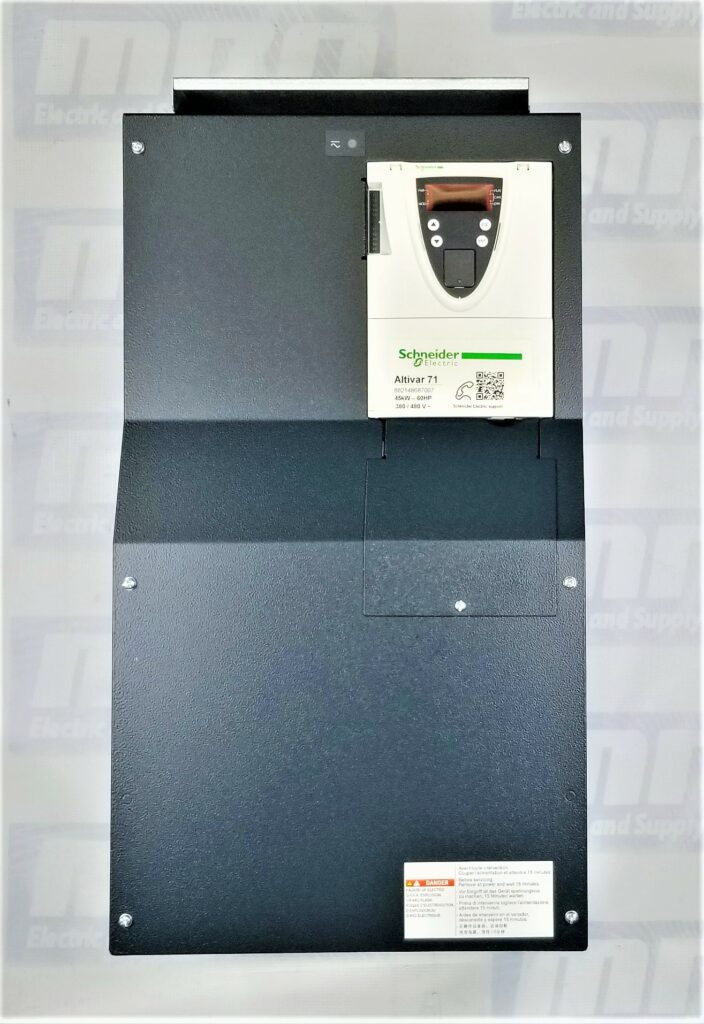
Frequency Control
The heart of VFD operation is the ability to control the motor’s frequency. In an AC motor, the speed is directly proportional to the frequency of the supplied power. Standard power from the grid operates at a fixed frequency (usually 60 Hz in North America and 50 Hz in most other regions), resulting in a constant motor speed when connected directly. However, VFDs can modify this frequency according to the desired speed, creating a dynamic system.
To adjust the frequency, VFDs convert incoming AC power into DC (Direct Current) using rectifiers, then generate a new AC output with a variable frequency through an inverter. This allows precise control over the motor’s rotational speed, ensuring it operates optimally under varying conditions.
Read More